Barite Beneficiation Plant & Equipment | Gravity & Flotation
ZONEDING MACHINE provides complete barite beneficiation solutions. Expert design, equipment (jigs, flotation cells), and turnkey plants to upgrade barite ore grade & specific gravity. Achieve API specs. Get Proposal!
Clueless About Barite Beneficiation? From Raw Ore to High-Quality Concentrate, Here Are the Key Steps!
Barite beneficiation involves processes like washing, crushing, grinding, gravity separation, or flotation to remove impurities (like quartz, calcite) and increase the barium sulfate (BaSO4) content and specific gravity, meeting specifications for drilling mud or other industrial uses.
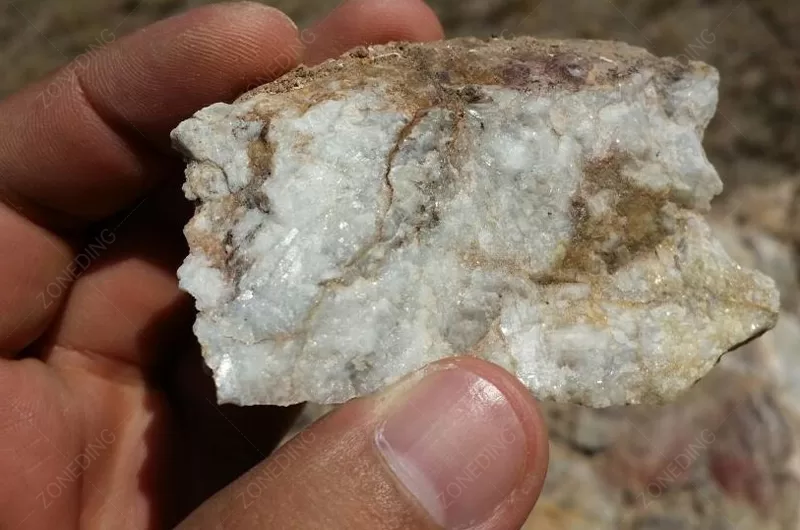
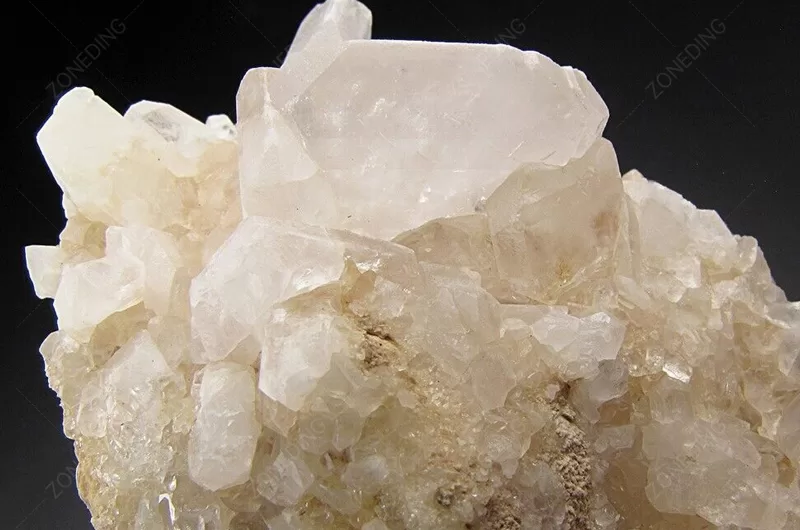
Transforming low-grade barite into a valuable product requires understanding the right steps and potential challenges. As experts at ZONEDING, with years supplying mineral processing equipment, we’ve seen what works. Let’s break down the journey from raw ore to high-quality concentrate.
This Article Will Tell:
- Why Beneficiate Raw Barite Ore?
- What are the Main Uses and Quality Requirements for Barite Concentrate? (Especially API Drilling Grade!)
- What are the Main Barite Beneficiation Methods, and How to Choose the Best for My Ore?
- What are the Core Challenges Affecting Barite Beneficiation? (e.g., Specific Gravity, Associated Minerals)
- What Key Equipment is in a Typical Barite Beneficiation Plant?
- How to Significantly Improve Barite Recovery and Specific Gravity via Process Optimization (Gravity or Flotation)?
- What Common Problems Occur in Barite Beneficiation, and How to Avoid/Solve Them? (Slime Handling is Key!)
- How to Get Customized Beneficiation Testing and Flowsheet Design for My Barite Ore?
Why Beneficiate Raw Barite Ore?
Beneficiation is essential to remove unwanted gangue minerals (like quartz, clay, calcite), increase the BaSO4 percentage and specific gravity (SG), meet buyer specifications (especially for drilling), and significantly increase the ore’s market value.
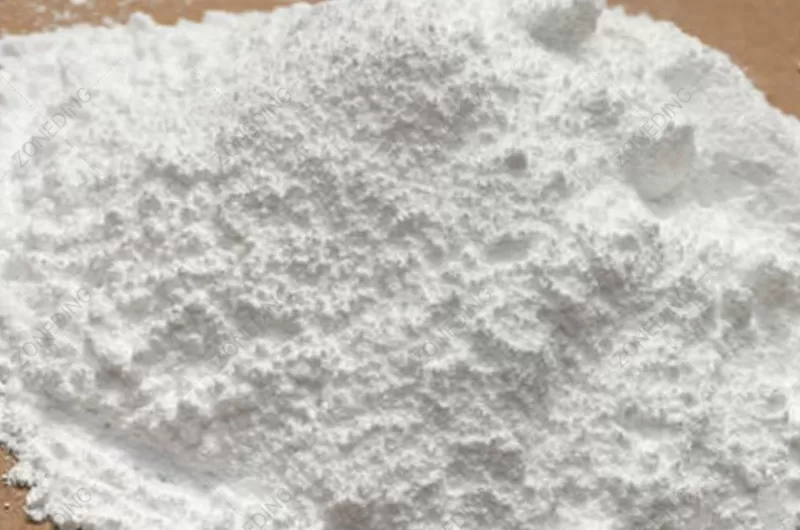
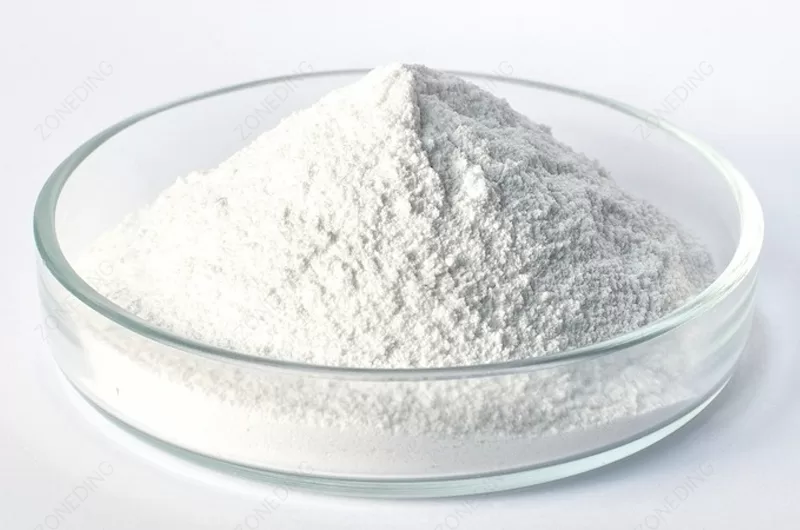
Raw barite ore rarely exists in a pure state. It’s typically mixed with various other minerals. These impurities lower the overall BaSO4 content and specific gravity, making it unsuitable for most high-value applications, particularly the demanding oil and gas drilling market. Beneficiation physically separates the valuable barite from these less valuable or detrimental minerals. This concentration process achieves several key goals:
- Increases BaSO4 Content: Buyers pay for BaSO4 percentage. Removing waste rock directly boosts this critical parameter.
- Boosts Specific Gravity: High specific gravity is the primary functional requirement for drilling mud barite. Removing lighter minerals like quartz (SG ~2.65) and calcite (SG ~2.71) is crucial to elevate the overall SG of the concentrate above the required thresholds (often >4.10 or >4.20 g/cm³).
- Meets Market Specifications: Different industries have different purity requirements. Beneficiation allows you to tailor the product quality to meet specific standards, like the stringent API (American Petroleum Institute) specifications for drilling grade barite.
- Economic Viability: Selling upgraded concentrate commands a much higher price than selling low-grade raw ore, making the mining operation profitable. It also reduces transport costs per unit of valuable material.
What are the Main Uses and Quality Requirements for Barite Concentrate? (Especially API Drilling Grade!)
The primary use is as a weighting agent in drilling fluids (API grade). Key API specs include high Specific Gravity (SG >4.10 or 4.20 g/cm³), high BaSO4 (>90%), controlled particle size, and low soluble alkaline earth metals (like Calcium < 250 ppm). Other uses include fillers, chemicals, and radiation shielding.
Understanding the end-use dictates the required quality. The overwhelming majority of barite produced globally goes into drilling fluids for the oil and gas industry.
API Drilling Grade Requirements
This is the largest market with the strictest, most standardized specifications. Barite increases the hydrostatic pressure of the drilling mud to prevent oil/gas blowouts, cool the drill bit, and carry cuttings to the surface. Key API 13A requirements typically include:
Parameter | Typical Requirement | Importance |
---|---|---|
Specific Gravity (SG) | > 4.10 g/cm³ or > 4.20 g/cm³ | Primary function: provides density/weight. |
Barium Sulfate (BaSO4) | > 90% (often higher) | Ensures the density is primarily from barite. |
Soluble Salts (e.g., Ca²⁺) | < 250 ppm | Prevents interference with mud chemistry. |
+200 mesh (75 μm) residue | < 3.0% | Controls coarse particles affecting mud flow. |
+325 mesh (45 μm) residue | Variable (e.g., 5-15%) | Controls overall particle size distribution. |
< 6 μm particles | Often monitored/limited | Affects rheology (flow properties) of the mud. |
Insight: Many focus only on SG and BaSO4, but failing the particle size distribution (PSD) or soluble calcium limits are common reasons for API rejection. If your ore has associated calcite (CaCO3) or gypsum (CaSO4), even high-purity barite might fail API specs due to calcium. We at ZONEDING have seen clients struggle with this specific issue.
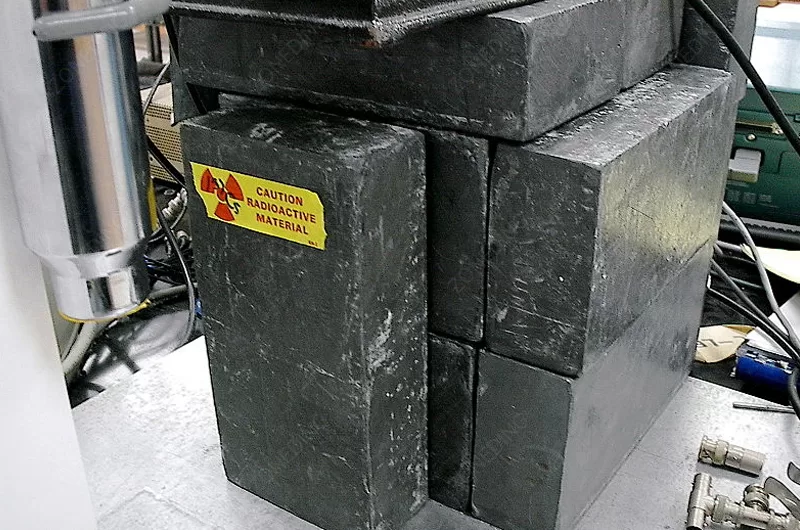
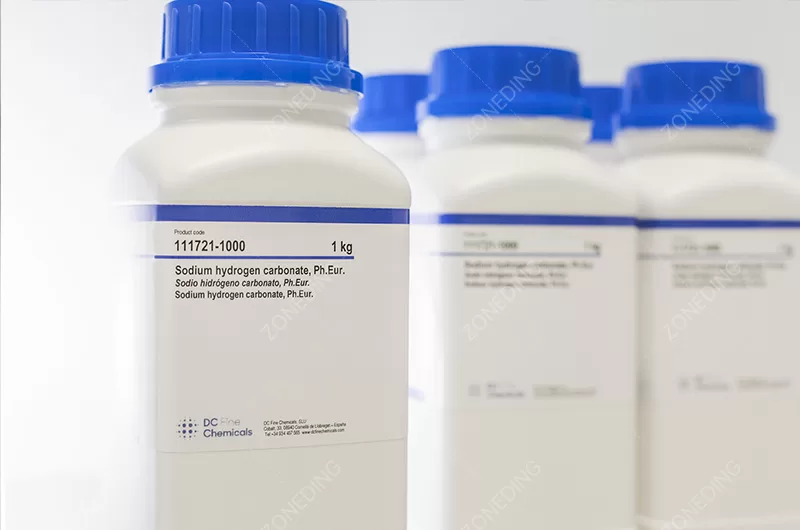
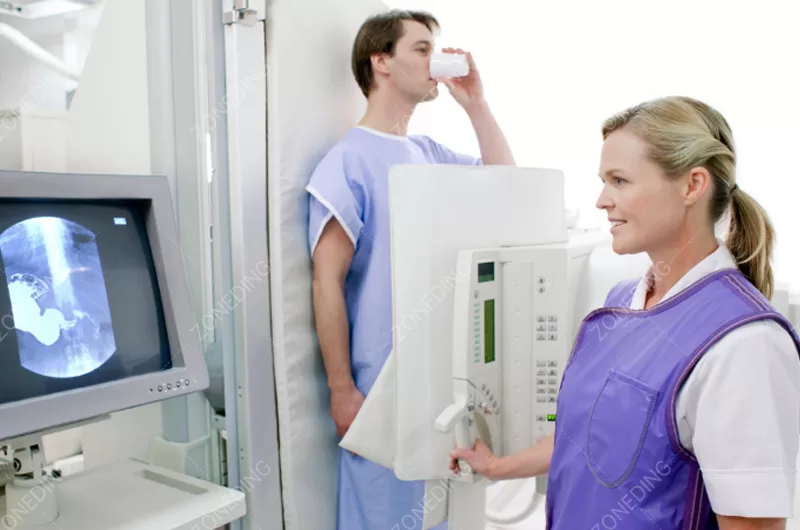
Other Uses
While drilling dominates, barite also finds use in:
- Fillers: Added to paint, plastics, and rubber to increase density, improve finish, or reduce cost. Quality requirements vary but often focus on brightness, particle size, and chemical inertness.
- Chemicals: Used to produce other barium chemicals (e.g., barium carbonate, barium chloride). Requires high BaSO4 purity.
- Medical: Highly purified barite is used for diagnostic medical tests (“barium meal”). Requires extreme purity.
- Shielding: Used in concrete for radiation shielding in hospitals and nuclear facilities due to its density.
What are the Main Barite Beneficiation Methods, and How to Choose the Best for My Ore?
Gravity separation (jigs, shaking tables, spirals) is most common, leveraging barite’s high SG. Flotation is used for fine-grained or complex ores where gravity isn’t effective. Washing/scrubbing removes clays. The best choice depends critically on ore mineralogy, liberation size, and associated minerals.
Choosing the right method, or combination of methods, depends entirely on your specific ore characteristics. There’s no single “best” way; it must be tailored.
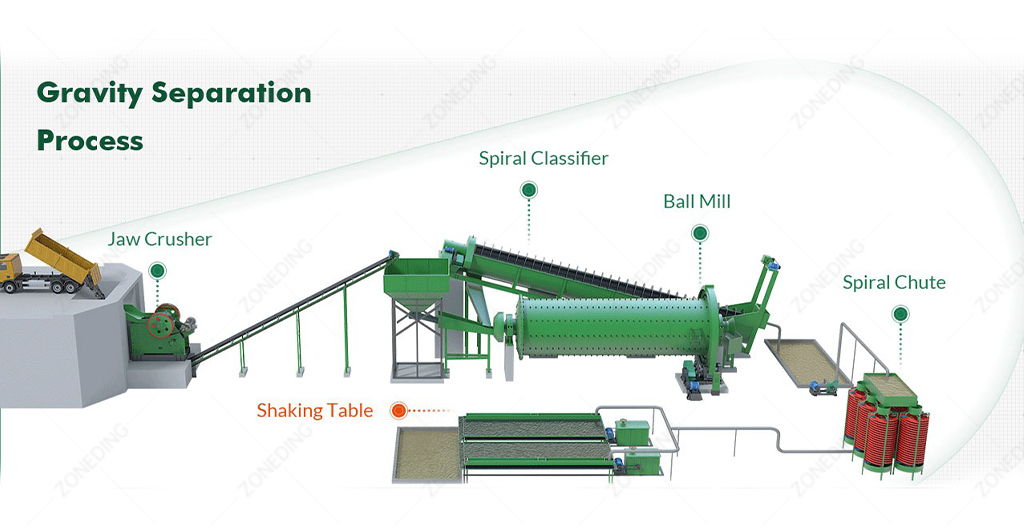
Gravity Separation
This is the workhorse for barite due to its high specific gravity (4.3-4.5 g/cm³) compared to common gangue minerals like quartz (~2.65), calcite (~2.71), and clays.
- How it Works: Uses differences in how minerals respond to gravity and fluid forces. Heavier particles settle faster or travel differently in flowing water or slurry.
- Common Equipment:
- Jigs: Use pulsating water current to stratify particles by density. Good for coarser particles (e.g., 2mm to 30mm).
- Shaking Tables: Use a riffled deck with differential motion and water flow to separate heavy from light. Effective for finer particles (e.g., 0.074mm to 2mm).
- Spiral Concentrators: Use slurry flowing down a spiral trough, where heavy particles concentrate towards the inner part. Good for intermediate sizes.
- Suitability: Best for ores where barite is relatively coarse-grained and liberated from gangue, and where there isn’t a significant amount of other heavy minerals with similar SG.
- Insight: Don’t rely on just one gravity method! Effective gravity circuits often use different equipment for different size fractions. For instance, screen the feed, send coarse material to jigs, and fine material to shaking tables. We often design circuits like this at ZONEDING.
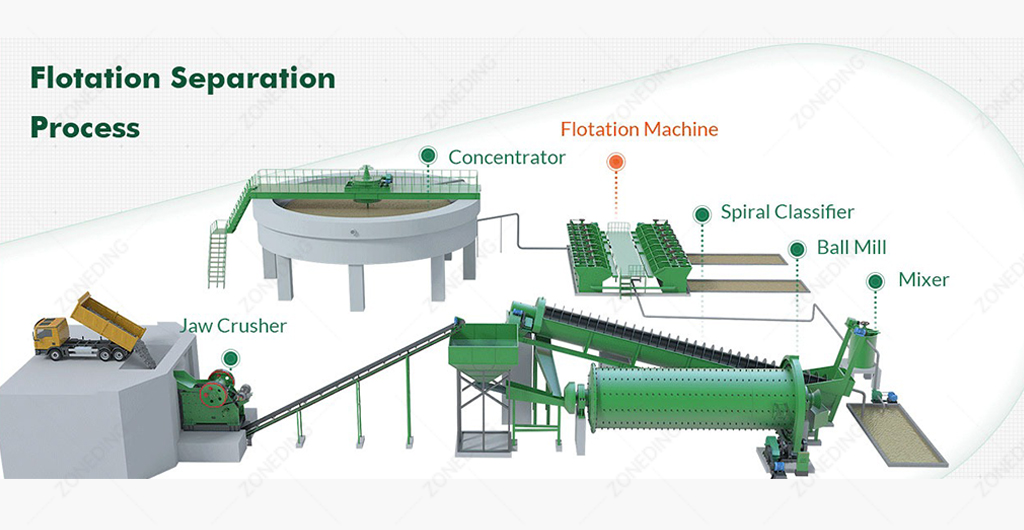
Flotation
Used when gravity separation isn’t sufficient.
- How it Works: Uses chemical reagents to make barite particles hydrophobic (water-repelling). Air bubbles are introduced, attach to the hydrophobic barite particles, and float them to the surface for collection as a froth. Gangue minerals remain water-wet and don’t float.
- Reagents: Typically uses fatty acids (like oleic acid) or alkyl sulfates as collectors for barite, often with pH modifiers and depressants for gangue minerals.
- Suitability: Necessary for very fine-grained ores where liberation requires grinding to sizes too small for effective gravity separation, or for ores with complex mineralogy (e.g., barite mixed with fluorite or sulfide minerals) where selective separation is needed.
- Insight: Flotation is more complex and expensive than gravity separation, involving higher capital costs (cells, reagent systems) and operating costs (reagents, power). It’s sensitive to slimes and water chemistry (especially Ca²⁺ ions). Only consider flotation if gravity methods truly cannot meet the required grade or recovery, or use it in combination (e.g., gravity pre-concentration followed by flotation polishing).
Washing and Scrubbing
Often a crucial pre-treatment step, especially for residual or clay-rich ores.
- How it Works: Uses water and mechanical action (e.g., in a log washer or rotary scrubber) to break down and wash away clay and slime coatings from coarser barite particles.
- Suitability: Essential for ores with significant clay content. Removing clay early improves the efficiency of all downstream processes (crushing, screening, gravity separation).
Method | Principle | Best Suited For | Key Equipment | Complexity/Cost |
---|---|---|---|---|
Gravity | Density Difference | Coarse/Medium liberated barite, simple mineralogy | Jigs, Tables, Spirals, Cones | Lower |
Flotation | Surface Chemistry | Fine-grained, complex ores, high purity needed | Flotation Cells, Reagent System | Higher |
Washing/Scrubbing | Clay Disintegration | Clay-rich ores | Log Washer, Rotary Scrubber | Low-Medium |
What are the Core Challenges Affecting Barite Beneficiation? (e.g., Specific Gravity, Associated Minerals)
The biggest challenges are managing the slimes generated due to barite’s softness, achieving clean liberation from gangue without over-grinding, and dealing with associated minerals that have similar densities or interfere with processing.
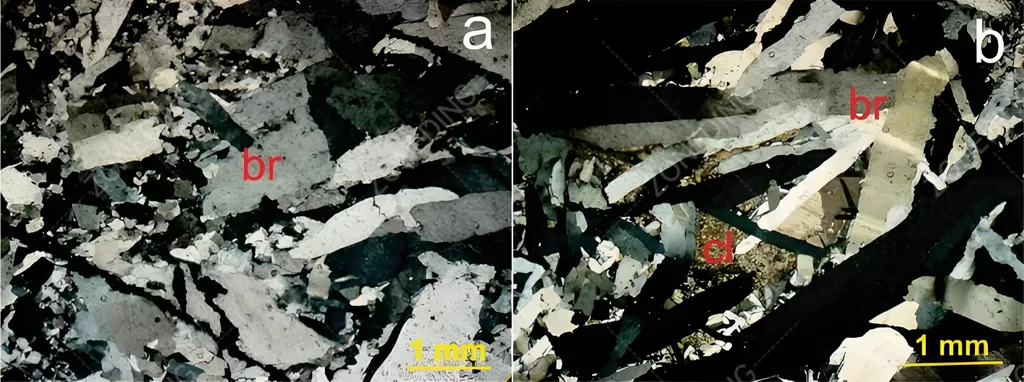
While barite’s high SG is an advantage, several factors complicate its beneficiation:
The Slime Problem: Barite’s Worst Enemy
Insight: This is often the issue we see. Barite is relatively soft (Mohs hardness 3-3.5). During crushing and especially grinding, it easily generates very fine particles (-10 μm), known as slimes. These slimes are detrimental because they:
- Increase Slurry Viscosity: Makes it harder for particles to settle according to density in gravity separators. Imagine trying to separate sand from pebbles in thick mud versus clear water.
- Coat Larger Particles: Slime coatings can prevent barite particles from responding correctly in gravity or flotation processes.
- Cause High Losses: Fine barite particles are easily washed away into the tailings stream, especially in gravity circuits, drastically reducing recovery.
- Interfere with Flotation: Slimes consume large amounts of expensive reagents and can hinder bubble-particle attachment.
Solution: Effective desliming before concentration is critical. This involves washing, scrubbing, and using classification equipment like hydrocyclones or high-frequency screens specifically designed to remove fines early in the process.
Liberation vs. Over-grinding
To separate barite from gangue, the ore must be ground fine enough to “liberate” the individual mineral particles. However, because barite is soft:
- Over-grinding Risk: Grinding too fine generates excessive slimes (see above).
- Gentle Grinding Needed: The goal is to grind just enough for liberation, not pulverize everything.
- Insight: Rod mills are often preferred over ball mills for barite because they tend to produce fewer extreme fines. Closed-circuit grinding (mill paired with a classifier) is essential to remove liberated particles quickly and prevent them from being over-ground.
Associated Minerals Challenges
The type and nature of minerals mixed with barite matter significantly:
- Similar Specific Gravity: Minerals like fluorite (SG ~3.2) or sometimes iron carbonates (siderite, SG ~3.9) can have densities close enough to barite to make gravity separation difficult.
- Interfering Minerals in Flotation: Minerals like calcite readily react with fatty acid collectors used for barite, requiring selective depressants or careful pH control. Sulfide minerals (like pyrite) might also be present and require separate removal steps (e.g., sulfide flotation first).
- Hard, Abrasive Gangue: While barite is soft, associated quartz (Mohs 7) is hard and abrasive, causing significant wear on crushers, mills, screens, and pumps.
What Key Equipment is in a Typical Barite Beneficiation Plant?
Planning to build a barite processing line? Knowing the essential machinery helps you budget and design effectively.
A typical plant includes: Feed Hoppers, Crushers (Jaw, Cone/Impact), Vibrating Screens, Washers (Log Washer/Scrubber if clayey), Grinding Mills (Rod/Ball), Classifiers (Hydrocyclones/Screens), Gravity Separators (Jigs, Tables, Spirals), possibly Flotation Cells, Thickeners, Filters, and Conveyors.
The specific equipment configuration depends heavily on the chosen process (gravity, flotation, or combined) and the ore characteristics, but a typical flow involves these stages and machines:
1. Crushing and Screening
- Purpose: Reduce large run-of-mine ore to a manageable size for washing or grinding.
- Equipment:
- Feeders: Vibrating grizzly feeders or apron feeders to control feed rate.
- Primary Crusher: Usually a Jaw Crusher for initial size reduction.
- Secondary/Tertiary Crusher (Optional): Cone crusher or impact crusher for further size reduction if needed.
- Vibrating Screens: To separate material by size, often sending oversized back for more crushing (closed circuit).
2. Washing and Desliming (If Needed)
- Purpose: Remove clay and slime coatings.
- Equipment:
- Rotary Scrubber or Log Washer: Vigorously washes and disintegrates clay lumps.
- Screens: Wash screens remove loosened fines.
- Hydrocyclones: Often used on finer fractions for efficient desliming.
3. Grinding and Classification
- Purpose: Grind the ore to liberate barite from gangue minerals. Control the particle size fed to separation.
- Equipment:
- Grinding Mills: Rod Mills (often preferred to minimize fines) or Ball Mills.
- Classifiers: Hydrocyclones are most common for wet classification. High-frequency screens can be used for fine screening. Operates in closed circuit with the mill.
4. Separation (Concentration)
- Purpose: Separate valuable barite from waste gangue.
- Equipment:
- Gravity Separators: Jigs (for coarser feed), Shaking Tables (for finer feed), Spiral Concentrators (intermediate sizes). Often used in combination for different size fractions.
- Flotation Cells: If flotation is used (for fines or complex ores), includes conditioning tanks (for reagent mixing) and banks of flotation cells (rougher, scavenger, cleaner stages).
5. Dewatering
- Purpose: Remove water from the final concentrate and tailings.
- Equipment:
- Thickeners: Large tanks allowing solids to settle, producing a thicker underflow slurry and clear overflow water for recycling.
- Filters: Filter presses or vacuum filters to remove more water from the thickener underflow, producing a filter cake (concentrate) suitable for handling and transport.
- Tailings Ponds/Dry Stack: For final disposal of waste material.
ZONEDING manufactures a wide range of this equipment, including crushers, screens, grinding mills, classifiers, and gravity separators, and we can help design a circuit tailored to your ore.
How to Significantly Improve Barite Recovery and Specific Gravity via Process Optimization (Gravity or Flotation)?
Focus on effective desliming, optimizing grinding for liberation without overgrinding, precisely tuning separator parameters (jig pulse, table settings, flotation reagents/pH), and implementing multi-stage cleaning circuits.
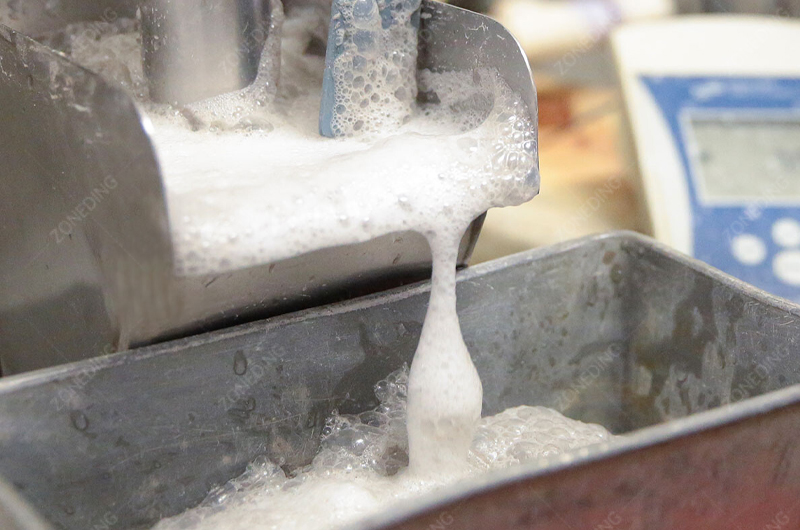
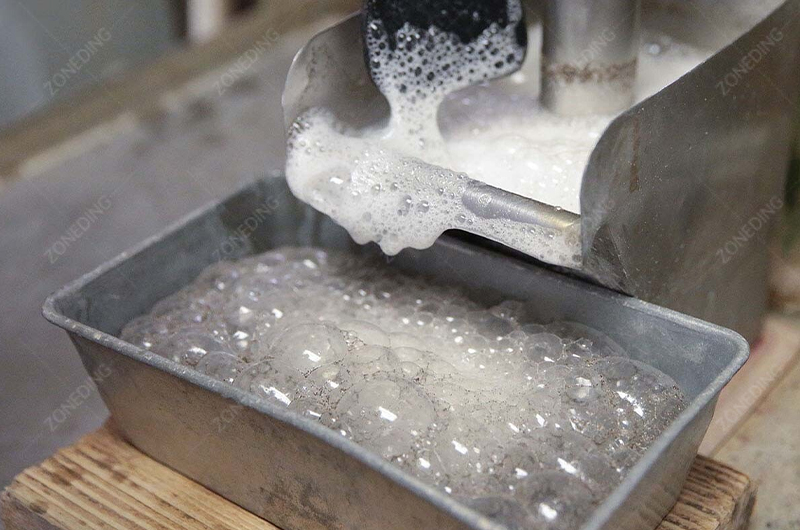
Getting the best performance requires attention to detail and continuous optimization across the circuit:
Effective Desliming is King
We cannot stress this enough. If you are using gravity separation or flotation, getting rid of slimes before the concentration stage is paramount.
- Actions: Implement efficient washing/scrubbing if needed. Use properly sized hydrocyclones or fine screens dedicated to slime removal. Don’t let fines build up in circuits.
Smart Grinding and Classification
Grind only as fine as necessary for liberation.
- Actions: Prefer rod mills if possible. Operate mills in closed circuit with efficient classifiers (hydrocyclones or screens). Monitor classifier performance closely to ensure a sharp cut size and minimize liberated barite returning to the mill. Avoid overloading the mill.
Tuning Gravity Separators
Small adjustments can yield big results.
- Jigs: Optimize the water pulsation cycle (stroke length and frequency). Insight: This is an art! The goal is fluidization without washing away fines. Different sizes need different settings. Modern air-pulsated jigs offer better control. Ensure consistent water pressure and feed rate.
- Shaking Tables: Adjust table slope, stroke length, frequency, and wash water volume to achieve the best separation band between barite and gangue. Feed density and particle size consistency are crucial.
Finesse in Flotation (If Used)
Flotation requires careful chemical management.
- Actions: Optimize reagent dosages (collector, depressant, activator, pH modifier) through testing. Control pulp pH precisely. Ensure adequate conditioning time. Monitor froth appearance. Water quality is critical – hardness (Ca²⁺, Mg²⁺) can severely affect fatty acid collectors.
Multi-Stage Circuits (Cleaning)
Don’t expect perfect separation in one pass.
- Actions: Implement rougher-scavenger-cleaner circuits.
- Rougher: Aims for high recovery, even if grade is moderate.
- Scavenger: Treats rougher tailings to recover remaining values.
- Cleaner: Treats rougher concentrate to achieve the final target grade, rejecting middlings (particles needing more grinding or separation). Multiple cleaning stages may be needed for high-purity products.
What Common Problems Occur in Barite Beneficiation, and How to Avoid/Solve Them? (Slime Handling is Key!)
Hitting roadblocks? Unexpected shutdowns or poor quality? Many plants face similar issues. Knowing them helps you prepare.
Frequent problems include poor recovery/grade due to slimes, inefficient classification causing downstream issues, high wear on equipment from abrasive gangue, feed inconsistencies upsetting the circuit, and difficulty meeting strict final product specifications.
Being aware of common pitfalls allows for proactive measures:
- The Slime Problem (Persistent Issue):
- Symptoms: Low recovery, low concentrate grade (especially SG), difficulty in dewatering, poor flotation performance.
- Solution: Prioritize washing/desliming stages. Use appropriate equipment (scrubbers, hydrocyclones). Ensure classifiers effectively remove fines. Consider specialized flocculants in thickeners if needed, but be cautious as they can affect water recycling.
- Inefficient Classification:
- Symptoms: Coarse material reporting to fine circuits (overloading tables/flotation), fine material returning to mill (overgrinding), unstable feed to separators.
- Solution: Select appropriately sized classifiers (cyclones/screens). Maintain them properly (cyclone apex/vortex finder wear, screen blinding/tears). Monitor performance regularly (sampling, efficiency calculations).
- High Equipment Wear:
- Symptoms: Frequent replacement of crusher liners, mill liners, screen decks, pump parts. High maintenance costs.
- Solution: Insight: Acknowledge abrasive gangue (like quartz). Select appropriate wear-resistant materials (high-chrome alloys, rubber, ceramics, polyurethane) during equipment specification. Implement a preventative maintenance schedule for wear parts.
- Feed Fluctuations:
- Symptoms: Unstable circuit performance, fluctuating concentrate grade/recovery.
- Solution: Use surge bins and reliable feeders (e.g., belt feeders, vibrating feeders) to ensure a consistent feed rate and composition to key stages like grinding and separation. Improve mine planning for ore blending if possible.
- Flotation Challenges (If Applicable):
- Symptoms: Low recovery/grade, high reagent consumption, unstable froth.
- Solution: Strict control over reagent dosage, pH, pulp density. Monitor water quality regularly (especially hardness). Ensure proper conditioning. Train operators well.
- Meeting Final Specifications (Especially API):
- Symptoms: Concentrate rejected by buyers despite good BaSO4/SG.
- Solution: Insight: Understand all critical parameters (PSD, soluble Ca, etc.). Implement grinding/classification strategies to control PSD. If soluble Ca is high due to gangue (calcite/gypsum), specific leaching steps might be needed (adds complexity/cost). Regular product quality analysis is essential.
How to Get Customized Beneficiation Testing and Flowsheet Design for My Barite Ore?
Send truly representative samples of your ore to a competent mineral processing laboratory or an experienced equipment manufacturer like ZONEDING. Comprehensive testing (mineralogy, grindability, gravity/flotation tests) is crucial to develop a reliable, customized flowsheet and select the right equipment.
Guesswork is expensive in mineral processing. Investing in proper testing upfront saves significant costs and headaches down the line. Here’s the process:
- Representative Sampling: This is the critical first step. The sample sent for testing must accurately reflect the ore body you intend to process in terms of grade, mineralogy, hardness, and variability. Poor sampling leads to misleading test results and flawed plant design.
- Ore Characterization: The lab will perform detailed analysis:
- Chemical Analysis: Determine BaSO4 content and identify potential penalty elements (e.g., silica, iron, calcium, heavy metals).
- Mineralogical Analysis: Identify all minerals present, their proportions, and importantly, how finely the barite is intergrown with gangue minerals (liberation characteristics). This dictates the required grinding size.
- Physical Properties: Determine ore hardness (Bond Work Index for grinding), specific gravity, and clay content/slime generation potential.
- Bench-Scale Beneficiation Tests: Small-scale tests simulate different process options:
- Crushing & Grindability Tests: Determine energy requirements for size reduction.
- Washing/Desliming Tests: Assess effectiveness of slime removal.
- Gravity Separation Tests: Using lab-scale jigs, tables, or heavy liquid separation (HLS) to determine the potential grade and recovery achievable by gravity methods at different particle sizes.
- Flotation Tests: Evaluate different reagent schemes, dosages, pH conditions, and grind sizes to determine optimal flotation performance if gravity is insufficient.
- Flowsheet Development: Based on the test results, engineers design the most technically sound and economically viable process flowsheet. This includes selecting the type and size of equipment for each stage.
- Pilot-Scale Testing (Optional but Recommended for Large Projects): Running a continuous pilot plant using a larger ore sample provides more reliable data on equipment performance, confirms the flowsheet, optimizes parameters, and generates bulk concentrate for end-user evaluation.
- Equipment Selection & Plant Design: The validated flowsheet guides the final selection and sizing of commercial-scale equipment.
At ZONEDING, we have the expertise and facilities to conduct comprehensive testing and develop tailored beneficiation solutions for your barite ore. Partnering with experienced professionals ensures your plant is designed for success from day one.