Disc Granulator
Applied Material:nPulverized coal, cement, clinker, limestone, shale, coal gangue, clay, fertilizer, etc.- Feeding Size:<50mm
- Capacity:4-24TPH
The Introduction of Disc Granulator

The Features of Disk Granulator
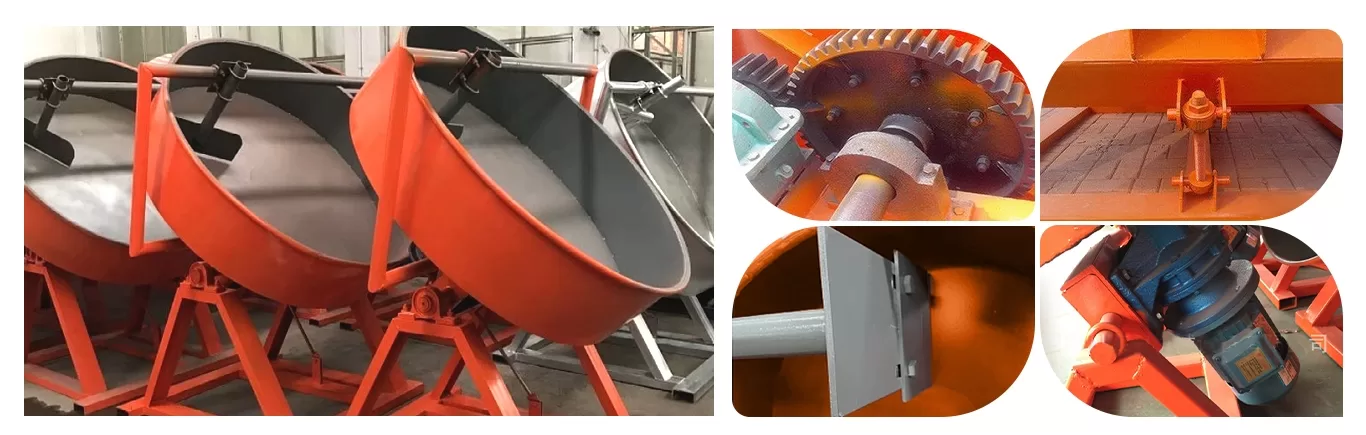
The Structures of Disc Granulator
Applications of Disc Granulator
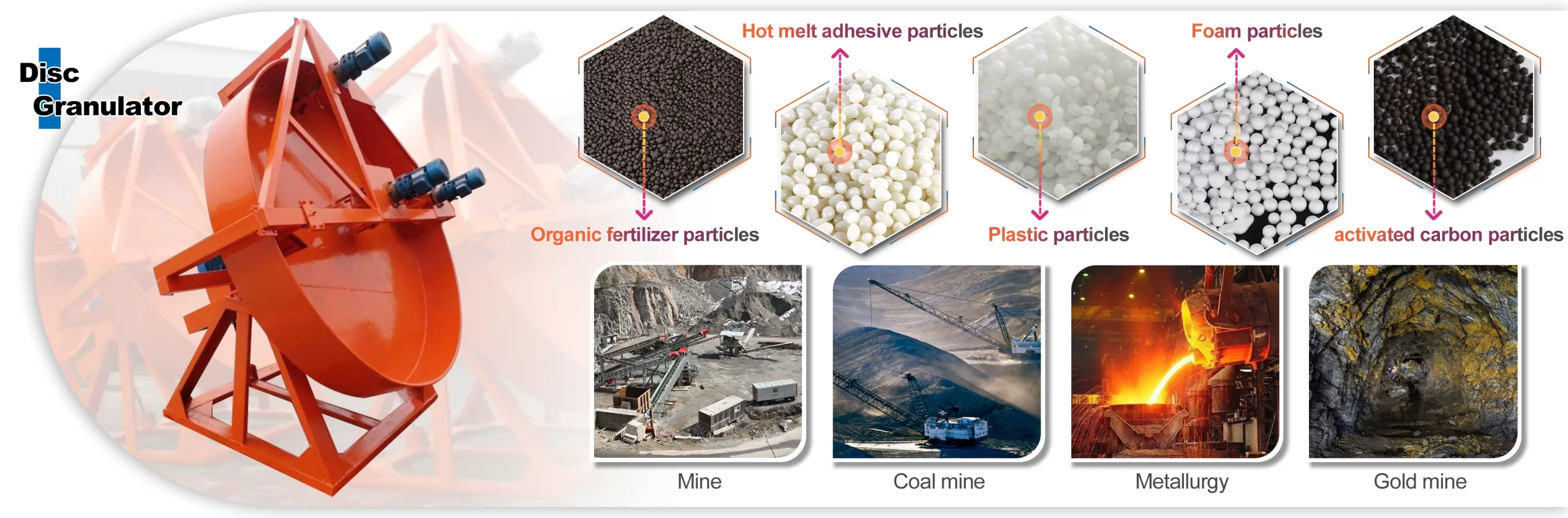
The Applications of Disc Granulator
The working principle of the disc granulator can be summarized as follows:
Disc Granulator Manufacturer
General Specification
Specification (m) | Rotation speed (r/min) | Production capacity (t/h) | Motor (kw) | Adjustment range of obliquity | Dimensions (m) | Total weight (t) |
Φ2.2 | 14.25 | 4-8 | 7.5 | 35-55 | 2.8×2.75×2.58 | 3.2 |
Φ2.5 | 11.81 | 5-10 | 7.5 | 35-55 | 3.2×2.3×3 | 3.6 |
Φ2.8 | 11.21 | 12-16 | 7.5 | 35-55 | 3.4×2.6×3.1 | 4.1 |
Φ3.0 | 11.3 | 15-18 | 11 | 35-55 | 3.7×2.7×3.3 | 4.8 |
Φ3.2 | 9.6 | 15-20 | 11 | 35-55 | 3.9×2.7×3.4 | 5.6 |
Φ3.6 | 9.1 | 18-24 | 15 | 35-55 | 4.3×3.1×4.0 | 7.2 |
Related Products
Ball Mill
Our ball mill are available in different styles and many models in each style to adapt to various grinding requirements.
Rod Mill
Our Rod Mill are available in different styles and numerous model sizes in each style to adapt to various grinding requirements. The rod mill is a grinding equipment that uses steel rods as the grinding media, widel…
Ceramic Ball Mill
Our Ceramic ball mill are available in different styles and numerous model sizes in each style to adapt to various grinding requirements. Ceramic ball mill, as a grinding tool for modern refinement industry, stands …
Flotation Machine
Our Flotation Machine are available in different styles and numerous model sizes in each style to adapt to various mineral separation requirements. Flotation machine is mainly used for separating gold, silver, coppe…
Magnetic Separator
Magnetic Separator is used to efficiently separate magnetic particles from non-magnetic materials in mineral processing, featuring a rotating drum design and customizable magnetic field strength for high-purity separation. …
Spiral Classifier
Spiral classifiers can grade different particles in ore slurry during the metal beneficiation process as well as deslime and dehydrate in the washing operation.
Jigging Separator Machine
Zoneding Machine supplies different types of jigging in mineral processing(such as fixed jig and mobile jig machine), the customized parameters for your requirements. A Mineral jigging machines is a gravity concent…
Gold Mine Wet Pan Mill
Wet pan mill is widely used in the gold mining industry and is one of the indispensable equipment in the modern gold mining industry. In addition, it can also be used for mining and processing other non-ferrous metals and precious metal ore…
Shaking Table
Our Shaking Table are available in different styles and numerous model sizes in each style to adapt to various mineral separation requirements. Shaking table is a kind of gravity beneficiation equipment, which is ma…
Hydrocyclone
Figure 1. Schematic representation of the spiral flow. Figure 2. Principal features of a hydrocyclone. ,
loading…
已经是到最后一篇内容了!