Trommel Screen
Applied Material:nscreening and grading of coal, refractory materials, river sand, sandstone block, heavy soda ash, light soda ash, activated carbon, metal ore powder, etc.- Feed Size: 50–150mm
- Capacity:12–150TPH
Introduction to Trommel Screen
How to Select a Suitable Trommel Screen?
The screen
Converter
The screening effect of the trommel screen
Applications of Trommel Screen
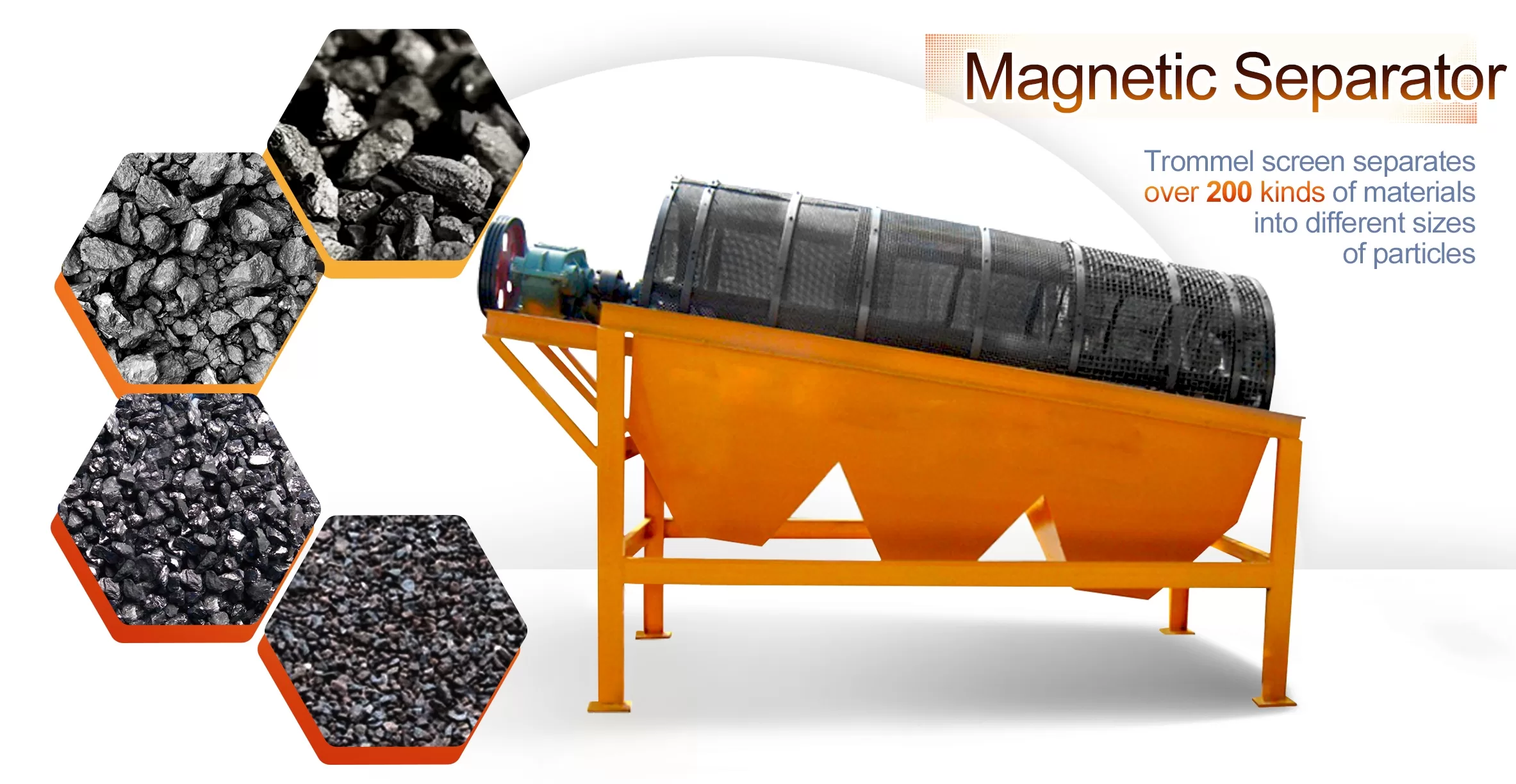
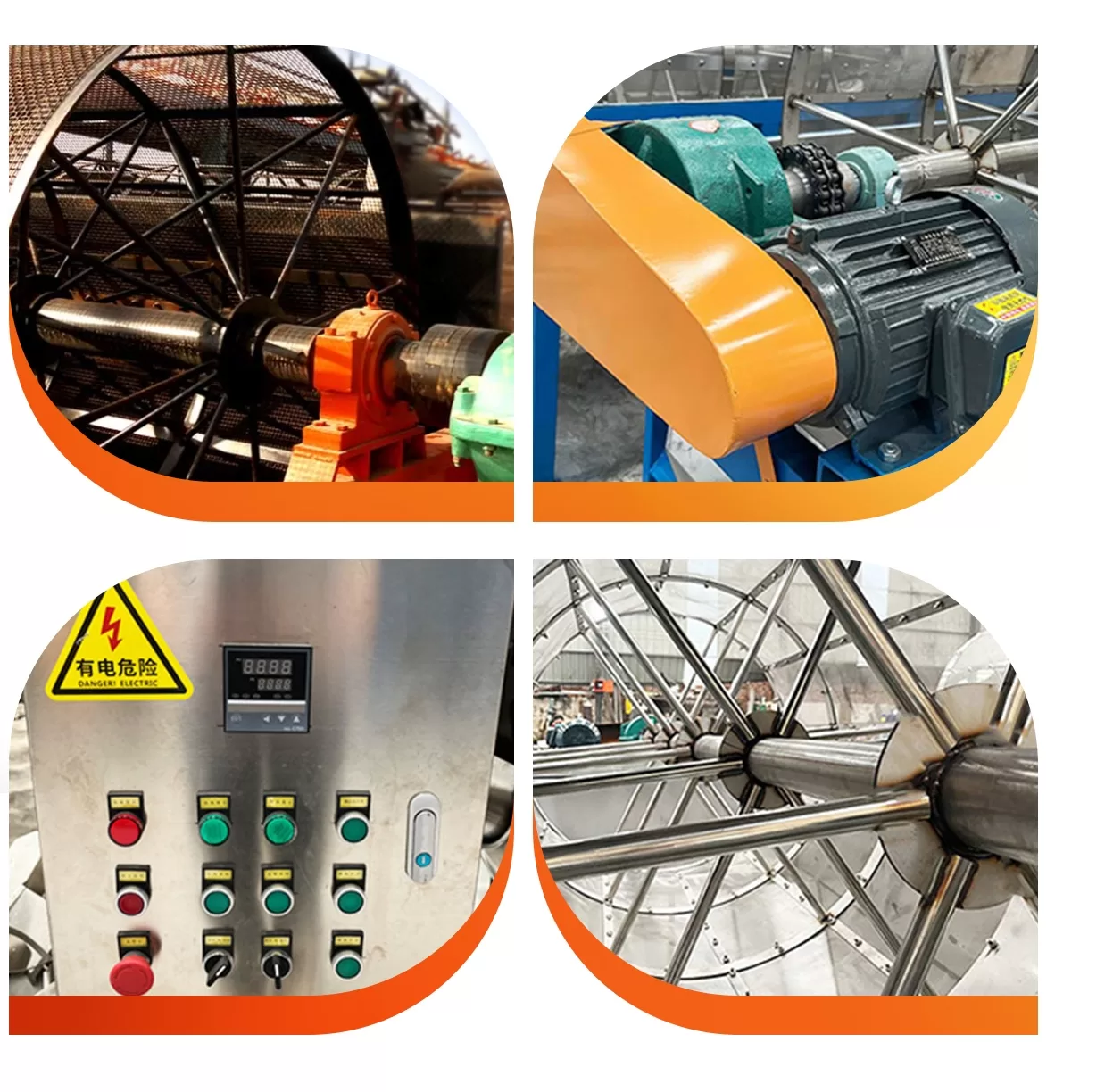

Performance Benefits
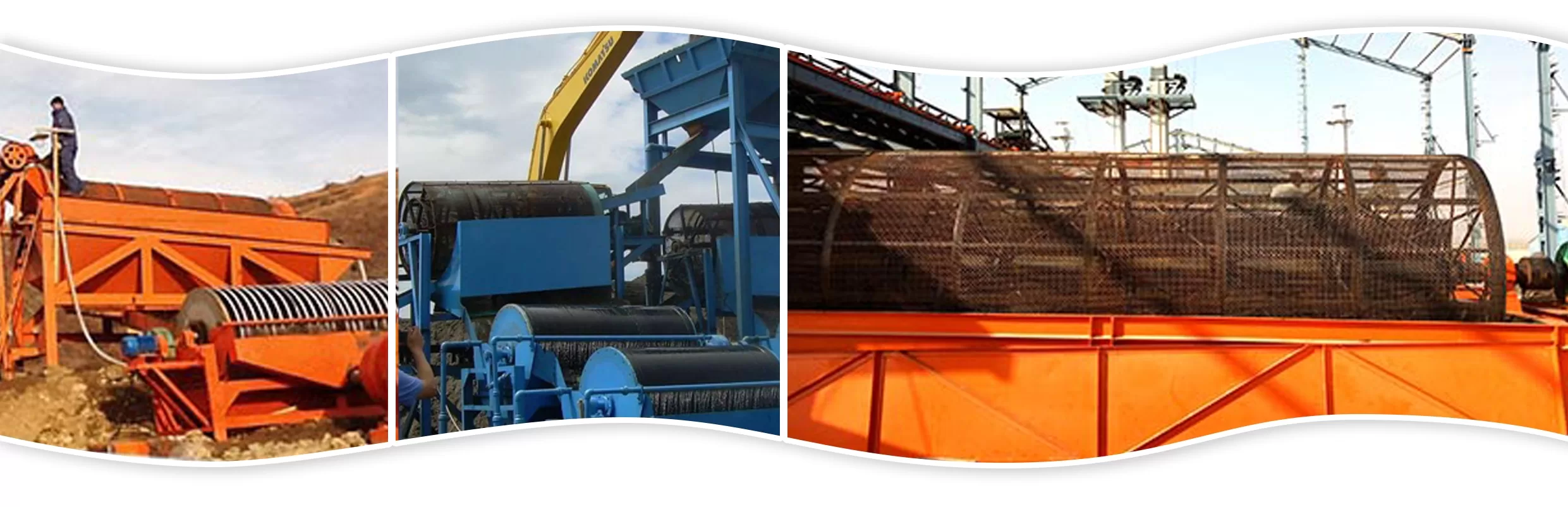
Working Principle
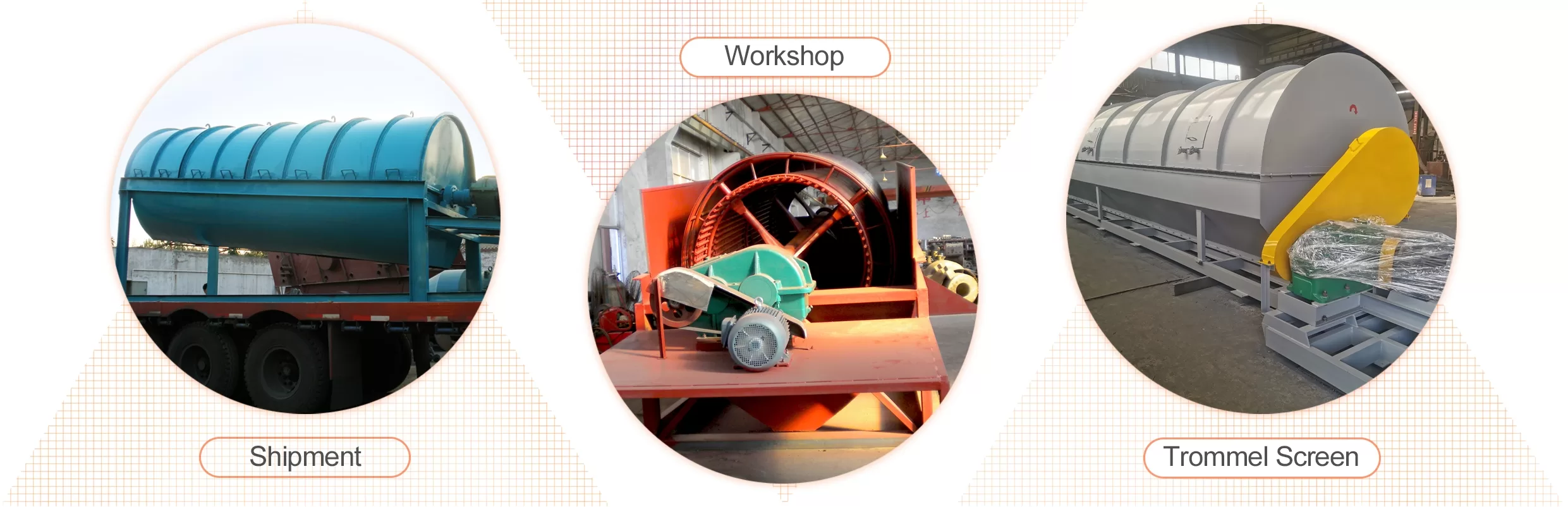
Common Faults of Trommel Screen and According Solutions
Faults | Causes | Solutions |
Poor-quality finished product from trommel screen | Screen hole is blocked. | Clean the screen hole regularly |
Low screen efficiency | The material is of high moisture. | Dewater the material ahead of time or increase the mesh of the screen hole. |
Low rotating speed of the trommel screen | The conveyor belt is loose. | Adjust the equipment transmission belt tightness timely to avoid harm to the machine service life. |
Hot bearing | The bearing needs to be oiled or cleaned. | Regularly clean and oil the bearing, replace the seal and check if the oil to the bearing meets the standards or not; replace the bearing if it is worn out seriously. |
Locked trommel screen roller | The seal sleeve maybe blocked. | Clean the shaft sleeve |
Irregular noise of the rotating trommel screen | Tightness degree of screen tightness, wearing degree of bearing, bolts to hold the parts, etc. | Pay regular check to screen, the bearings, bolts and other parts and timely adjust them according to standards. |
Classic Case
Customer Feedback
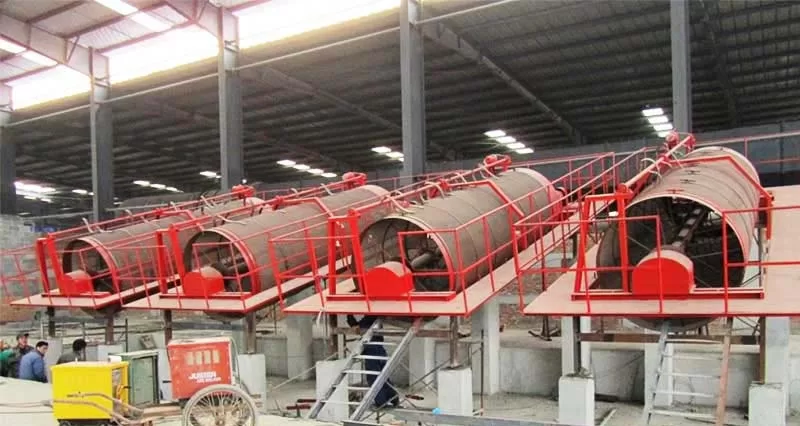
Trommel Screen Manufacturer
General Specification
Model | Yield(m³/h) | Power (kw) | |
Sieve hole(2mm) | Sieve hole(30mm) | ||
YTS1230 | 12 | 100 | 5.5 |
YTS1240 | 14 | 120 | 5.5 |
YTS1250 | 15 | 140 | 5.5 |
YTS1530 | 18 | 150 | 5.5 |
YTS1540 | 18 | 150 | 7.5 |
YTS1550 | 20 | 180 | 11 |
YTS1560 | 22 | 200 | 11 |
YTS2040 | 25 | 250 | 15 |
YTS2050 | 30 | 300 | 15 |
YTS2060 | 35 | 350 | 18.5 |
Related Products
Ball Mill
Our ball mill are available in different styles and many models in each style to adapt to various grinding requirements.
Rod Mill
Our Rod Mill are available in different styles and numerous model sizes in each style to adapt to various grinding requirements. The rod mill is a grinding equipment that uses steel rods as the grinding media, widel…
Ceramic Ball Mill
Our Ceramic ball mill are available in different styles and numerous model sizes in each style to adapt to various grinding requirements. Ceramic ball mill, as a grinding tool for modern refinement industry, stands …
Flotation Machine
Our Flotation Machine are available in different styles and numerous model sizes in each style to adapt to various mineral separation requirements. Flotation machine is mainly used for separating gold, silver, coppe…
Magnetic Separator
Magnetic Separator is used to efficiently separate magnetic particles from non-magnetic materials in mineral processing, featuring a rotating drum design and customizable magnetic field strength for high-purity separation. …
Spiral Classifier
Spiral classifiers can grade different particles in ore slurry during the metal beneficiation process as well as deslime and dehydrate in the washing operation.
Jigging Separator Machine
Zoneding Machine supplies different types of jigging in mineral processing(such as fixed jig and mobile jig machine), the customized parameters for your requirements. A Mineral jigging machines is a gravity concent…
Gold Mine Wet Pan Mill
Wet pan mill is widely used in the gold mining industry and is one of the indispensable equipment in the modern gold mining industry. In addition, it can also be used for mining and processing other non-ferrous metals and precious metal ore…
Shaking Table
Our Shaking Table are available in different styles and numerous model sizes in each style to adapt to various mineral separation requirements. Shaking table is a kind of gravity beneficiation equipment, which is ma…
Hydrocyclone
Figure 1. Schematic representation of the spiral flow. Figure 2. Principal features of a hydrocyclone. ,
loading…
已经是到最后一篇内容了!