Mobile crusher plant combines several equipment components into a single unit, which enables efficient and flexible operations in various locations. It is designed for crushing various types of materials on-site , such as rocks, ores, and construction waste, into smaller sizes for further processing or recycling.
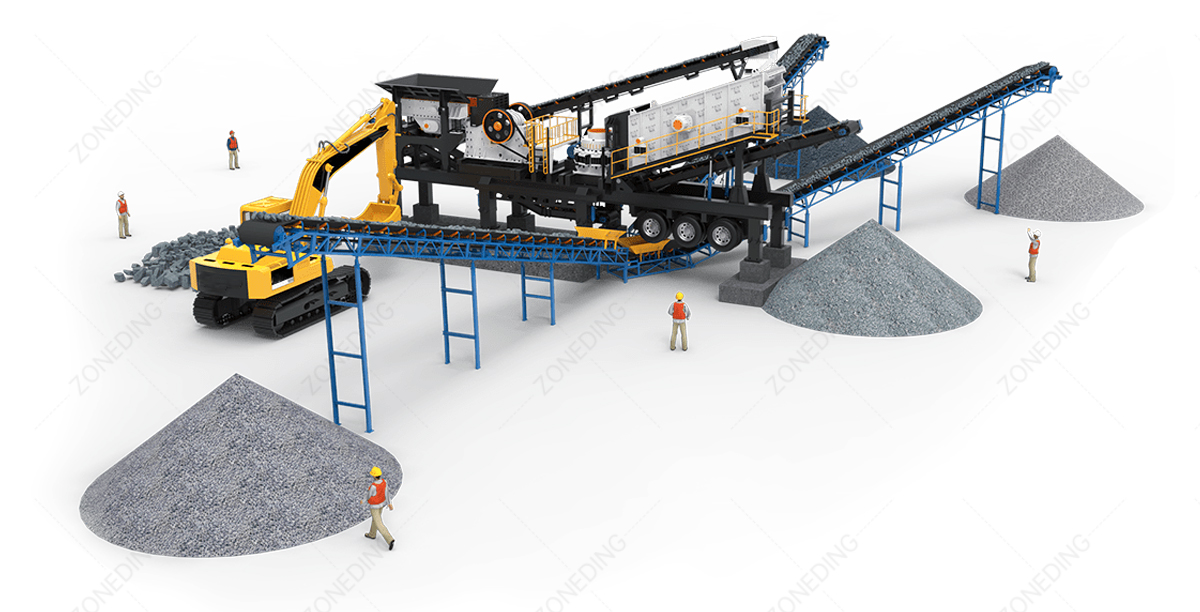
Hot-sale Mobile Crushing Plant – 4 in 1 Unit
We have launched the popular ZDY4 mobile crushing plant, designed for efficient processing of materials under 100 tph. The mobile crushing solution has combined advanced technology with compact design, making it ideal for various applications in construction and mining. With its mobility and high productivity, the ZDY4 ensures that you can easily transport and set up the plant at different job sites, while maintaining optimal performance.
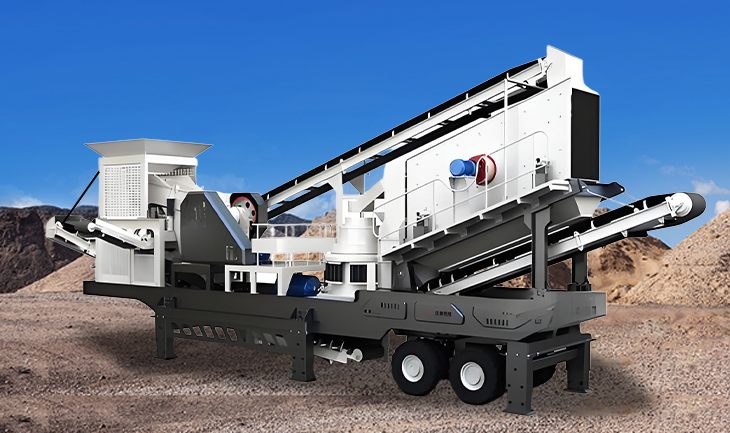
ZDY4 Wheeled Mobile Crushing Plant – Jaw Crusher + Impact Crusher
- Capacity: 50, 80, 100, 120tph
- Configuration: vibrating feeder, jaw crusher, Impact Crusher and vibrating screen.
- Finial Particle Size: 0-5mm, 5-10mm, 10-20mm, 20-40mm etc
- Applicable Materials: granite, marble, basalt, iron ore, river pebbles
- Main Application: supply aggregate for construction industry, especially for infrastructure construction, like roads and buildings.
Key Benefits of APY4 Mobile Crusher for Your Crushing Business
Easily switch between primary and secondary crushing modes to handle diverse kinds of materials.
Tailor capacity (50-120 t/h) and output specifications to your exact project requirements.
Achieve higher crushing ratios (up to 40% improvement) while reducing operational downtime.
4 in 1 Mobile Crusher Plant - Wheeled Chassis Type | ||||
---|---|---|---|---|
Model | ZDY4-46J2512J-S3 | ZDY4-46J900C-S3 | ZDY4-57J110C-S3 | ZDY4-69J132C-S3 |
Productivity(t/h) | 30 | 50 | 80 | 100-120 |
Vibrating Feeder | ||||
Model | ZDG-0824Z | ZDG-0824Z | ZDG-0930Z | ZDG-9538Z |
Primary Stone Crusher | ||||
Model | ZDJ-4060E | ZDJ-4060E | ZDJ-5075E | ZDJ-6090E |
Type | Jaw crusher | Jaw crusher | Jaw crusher | Jaw crusher |
Secondary Stone Crusher | ||||
Type | Jaw crusher | Cone crusher | Cone crusher | Cone crusher |
Model | ZDJ-2512X | ZDC-900Y | ZDC-110C | ZDC-132C |
Vibrating Screen | ||||
Model | ZDS-1548Y3 | ZDS-1548Y3 | ZDS-1848Y3 | ZDS-1848Y3 |
Belt Conveyor | ||||
Vehicle mounted belt conveyor | Yes | Yes | Yes | Yes |
Mobile Crusher Plants With Different Chassis For Selection
According to the chassis type, there are two types of mobile crushing and screening plants for sale in ZONEDING, including tracked type and wheeled type. Each type can be equipped with various crusher hosts, like mobile jaw crusher, mobile cone crusher plant, and mobile impact crusher plant.
Versatile Mobile Crushing Solutions for Diverse Applications
Demand for versatile and efficient crushing solutions is high. Choosing the right portable crusher plant is crucial for maximizing productivity and profitability across industries. Below are some on-site mobile crushing solutions for your reference.
The versatility of mobile crushing solutions is crucial for meeting the diverse needs of various industries and applications. The mobile crushing solutions mentioned above are all for large-scale crushing projects exceeding 100 tons per hour. If your project is relatively small, don't worry, ZONEDING also manufactures small mobile crushing and screening equipment to meet your crushing needs.
Small Mobile Crushing Plant Suitable for Your Projects – 30~50 tph
ZONEDING is proud to customize the crushing solutions that are appropriate for efficient and effective small-scale crushing tasks. If your budget for starting mini mobile crusher plant business is limited, it will be your best choice. With options for both crawler and wheeled types, the small mobile crusher plant is versatile and adaptable to a variety of working environments.
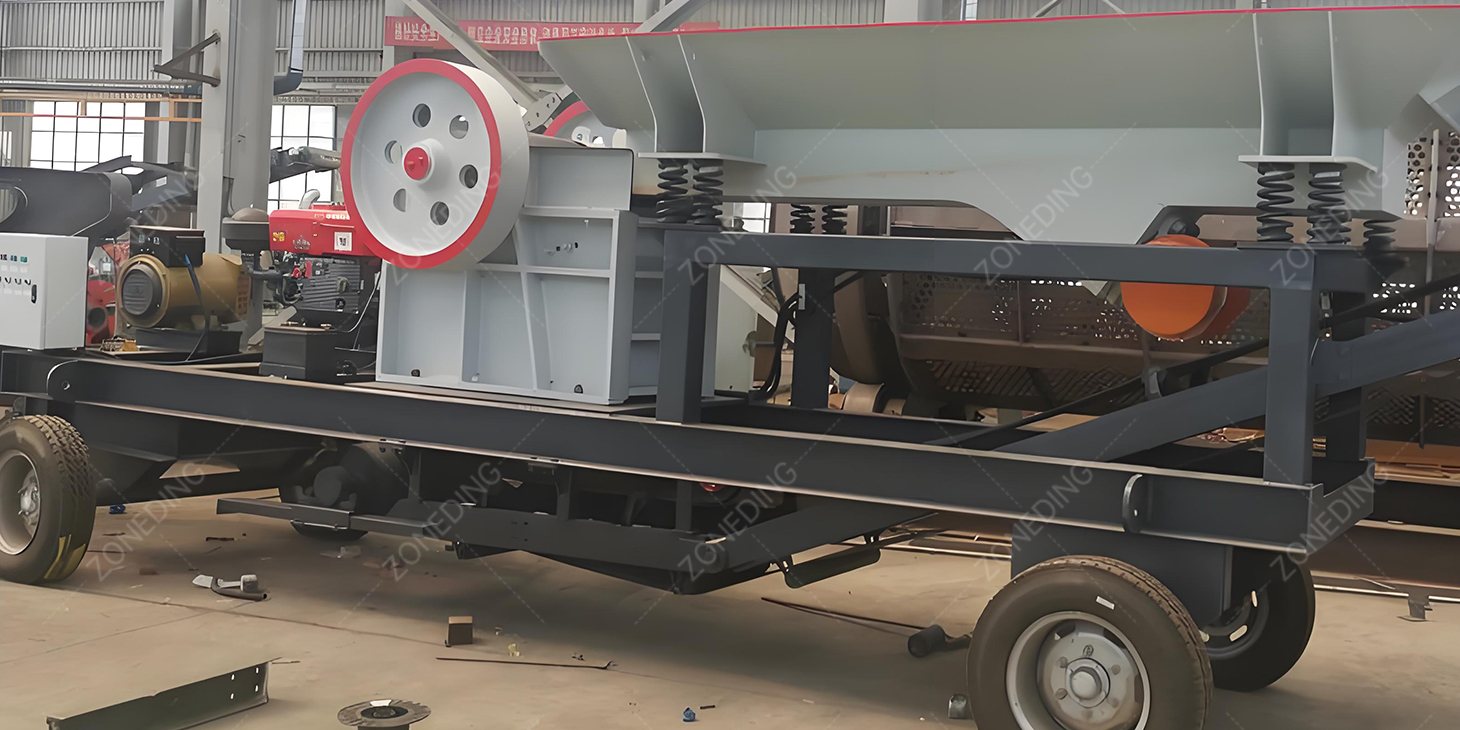
How Does A Mobile Crushing Plant Work?
The mobile crushing plant consists of several components, like crushers, feeders, and screens. These key components work in harmony to crush and screen materials on-site. Here is an overview of how the mobile crusher plant work:
Reasons To Choose Mobile Crusher Plant from Us
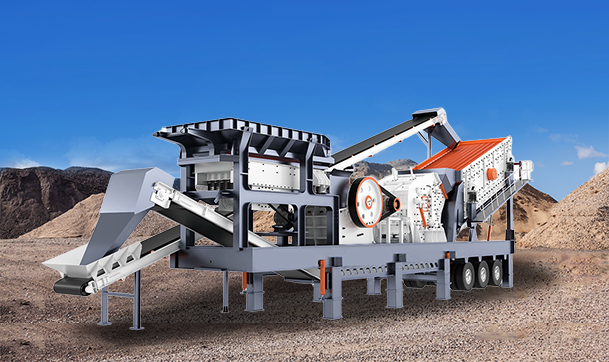
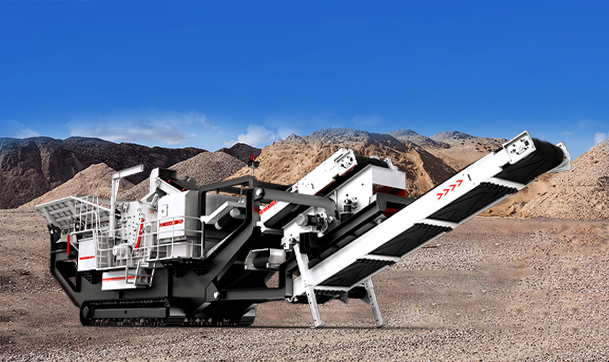
From the beginning of the production of portable crusher for sale, we have a sound evaluation mechanism, and we also have people to follow up the production process of the mobile screen crusher, strictly follow the use of high-quality materials and components, and effective inspection and testing to ensure that each mobile crushing plant meets the required quality standards.
Mobile crusher plants prioritize safety with features like hydraulic release mechanisms to prevent damage from uncrushable materials and emergency stop buttons for quick shutdown in case of emergencies.
The ZONEDING mobile crusher plant for sale is designed to have a compact and space-saving footprint, making it suitable for both urban and remote areas. It comes with integrated features such as a vibrating feeder, pre-screening system, and conveyor belts, which enhance the overall efficiency and productivity of the crushing process.
Our mobile crusher equipment is designed with noise reduction and emissions control in mind, aligning with environmental regulations and contributing to a quieter, more sustainable operation.
Most importantly, they are designed with ease of maintenance and repair in mind, with easy access to components and easy access to critical areas for inspection and repair, making them very cost effective.
We provide you with comprehensive support services, include 24/7 technical assistance and training. It can ensure smooth operation and minimal downtime.
In order to ensure the safe and smooth operation of the customer’s mobile crushing plant, considering the degree of wear and tear, our company specially provides our customers with high-quality original wearing parts supply, to solve the customer’s worries.
These advantages have made ZONEDING mobile crushing solutions a great option for many construction projects. As a leading mobile crusher plant manufacturer, ZONEDING offers a variety of portable crusher machine models to meet diverse project requirements. It is necessary for you to have a better understanding of each one, eapecially their features, charstaeristics, and advantages.
Features and Advantages of Mobile Crushing Machine
How to Choose A Right Mobile Crushing Plant?
01
Specify Your Needs.
First, you need to determine your needs, you need to know clearly what kind of project you are buying this mobile crusher plant for because there are more kinds of mobile crushing plants, different kinds also have different fields of application, so you must contact your engineer to negotiate your needs before asking for a quotation.
02
Know The Capacity.
Capacity is a very important factor, which is not only related to the production capacity of the portable crusher plant but also closely related to the price of the mobile crushing plant. Theoretically, the larger the capacity of the machine, the higher the portable crusher price will be. To avoid waste, just tell us your production requirements and we will recommend suitable portable crushing plant for your project.
03
Determine Right Mobile Crusher Manufacturers.
Choosing the right mobile crushing plant manufacturer is crucial, as it relates to quality, customization, support, and compliance. Reputable manufacturers provide reliable and durable equipment that meets requirements, possess technical expertise, offer comprehensive after-sales service and spare parts, and ensure safety and environmental compliance.
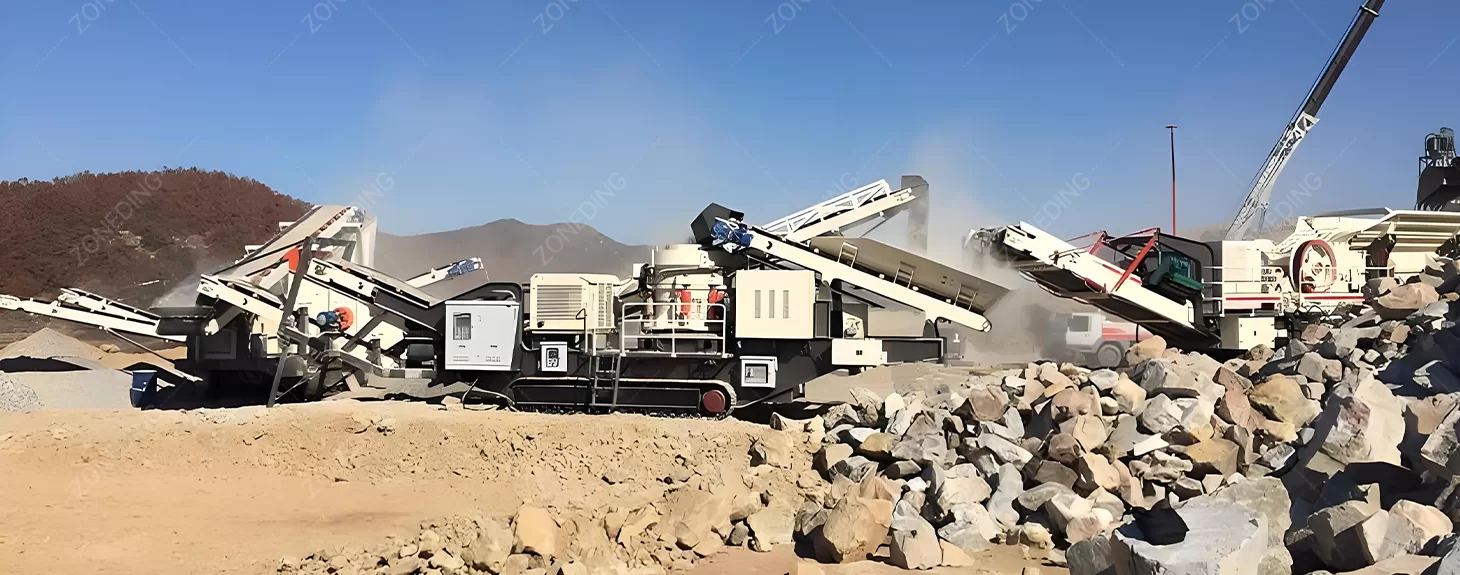
Knowing how to choose the right mobile crushing plant, I believe you already have a choice of your favorite mobile crusher and screening plant in mind. The next step is to consider the mobile screening plant price, so many mobile crusher plant manufacturers on the market, how can we talk about a reasonable price?
Tips To Help You Get A Reasonable Quote!
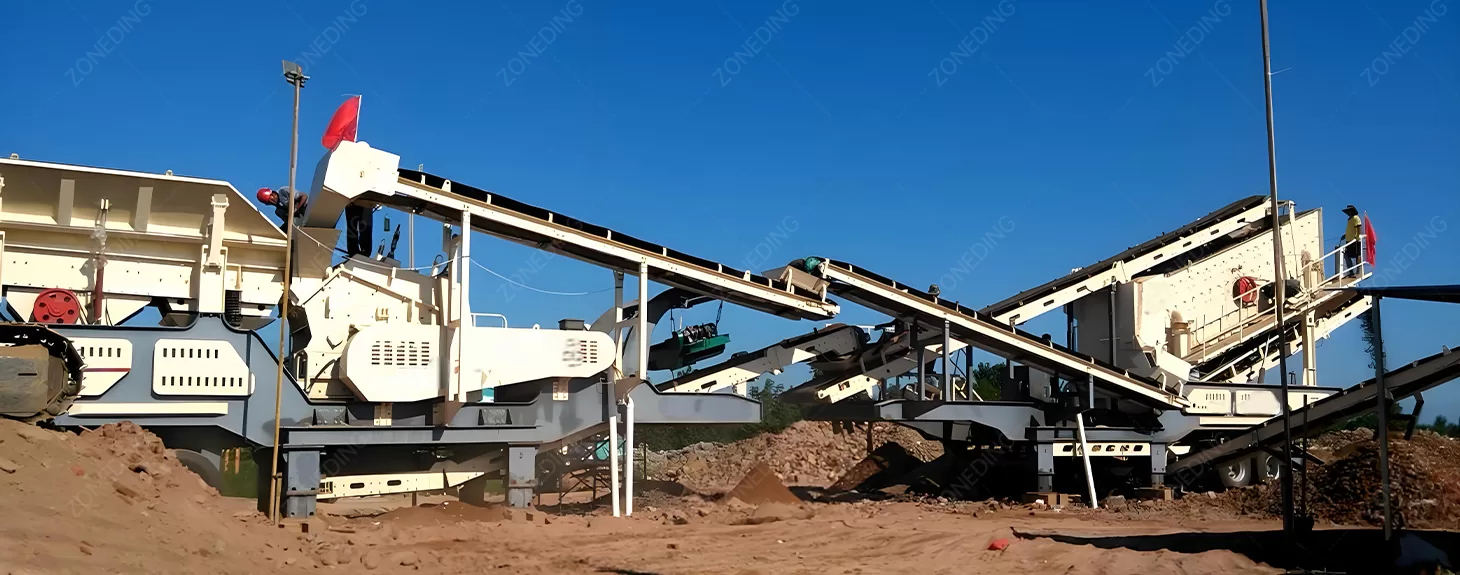
Everyone is the same, the first thing you do when buying something is to ask for a quote, while the mobile crusher plant price in turn is absolutely related to many factors, such as the location of the project, the type of product, and the size of the venue.
Therefore, before you want to be subject to specific prices, the user needs to figure out the things mentioned above. If possible, you can also write down the project local climate conditions, air pressure, voltage, etc., the more detailed, we can provide an accurate program to determine which product, which configuration is suitable for your project. Here are a few steps to help you inquire about the most real and accurate mobile screening plant price.
This is the first important thing, the stone mobile crusher plant belongs to large equipment, if you find a mobile crush plant supplier, the quality of thestone crushing plantsand the follow-up service can not be guaranteed. So you need to search Google, find more than 5 suppliers of mobile crushing machine, and make a strict and careful comparison.
After you have found several mobile crushing unit suppliers, the next thing you need to do is to examine the qualifications and capabilities of these mobile crusher machine suppliers. If possible, it is best to visit the factory, from the size of the vendor, staff, production technology, testing, shipping, etc. can determine the reliability of the vendor.
After visiting the plant, when discussing ZONEDING's crusher plant price, analyze the quote composition (tech, materials, patents, service) against expectations. Most importantly, review past customer feedback; real feedback best reflects product performance.After visiting the plant, when discussing ZONEDING's crusher plant price, analyze the quote composition (tech, materials, patents, service) against expectations. Most importantly, review past customer feedback; real feedback best reflects product performance.
After these three steps, you will surely find the right portable crusher plant for your project, and you will also get a good offer.
But the investment of the portable crusher plant is not simply buying and operating the portable crushing and screening plants, besides these, there are also maintaining the product, exploring more possibilities of the product and so on.
Therefore, we not only need to pay attention to the offer of this mobile crushing plant, but also you need to consider the following things in order to make the investment in mobile crushing plant more money.
Maximize The Benefits Of Investing In Mobile Crushing Plant
Everyone is the same, the first thing you do when buying something is to ask for a quote, while the mobile crusher plant price in turn is absolutely related to many factors, such as the location of the project, the type of mobile crushing station, and the size of the venue.
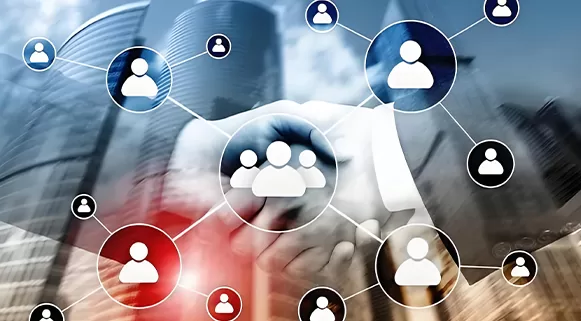
Seek diversified market opportunities:
In addition to the regular building and road construction market, seeking market opportunities in other areas can increase profits. Consider cooperating with related industries, such as quarries, waste recycling and earthmoving, to broaden the scope of application of products and improve portable crusher plant utilization. If necessary, you can also consider the option of selling the portable crusher plant at the end of the project or renting it out to someone in need. This is also a gain.
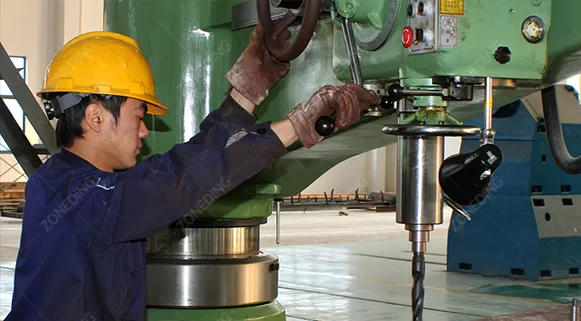
Pay attention to market trends and technological innovation:
Pay close attention to industry trends and technological innovation. Keep abreast of the latest mobile screening and crushing equipment technology and equipment improvements to stay competitive and meet customers’ changing needs. Upgrade equipment and introduce advanced technology at the right time to improve production efficiency and product quality.
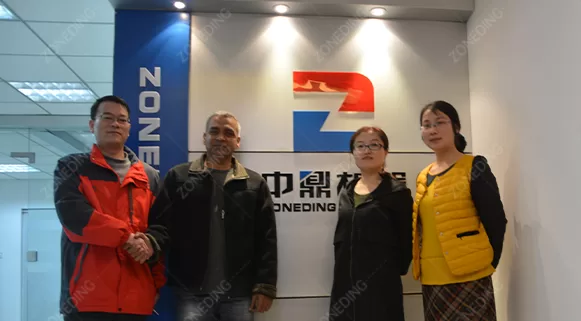
Pay attention to market trends and technological innovation:
Pay close attention to industry trends and technological innovation. Keep abreast of the latest mobile screening and crushing equipment technology and equipment improvements to stay competitive and meet customers’ changing needs. Upgrade equipment and introduce advanced technology at the right time to improve production efficiency and product quality.
In short, the more information you give, the more accurate the solution we give and the more detailed the price will be. And you will get many benefits after using the mobile crushers and screeners. If you are looking for a cost-effective mobile crusher station, contact us we can provide you with a free proposal according to your project needs.
In addition to mobile crushing plant, fixed crushing plant is also a product often asked by customers, the following briefly popularize fixed crushing plant to you.
Related Products – Stationary Crushing Plant
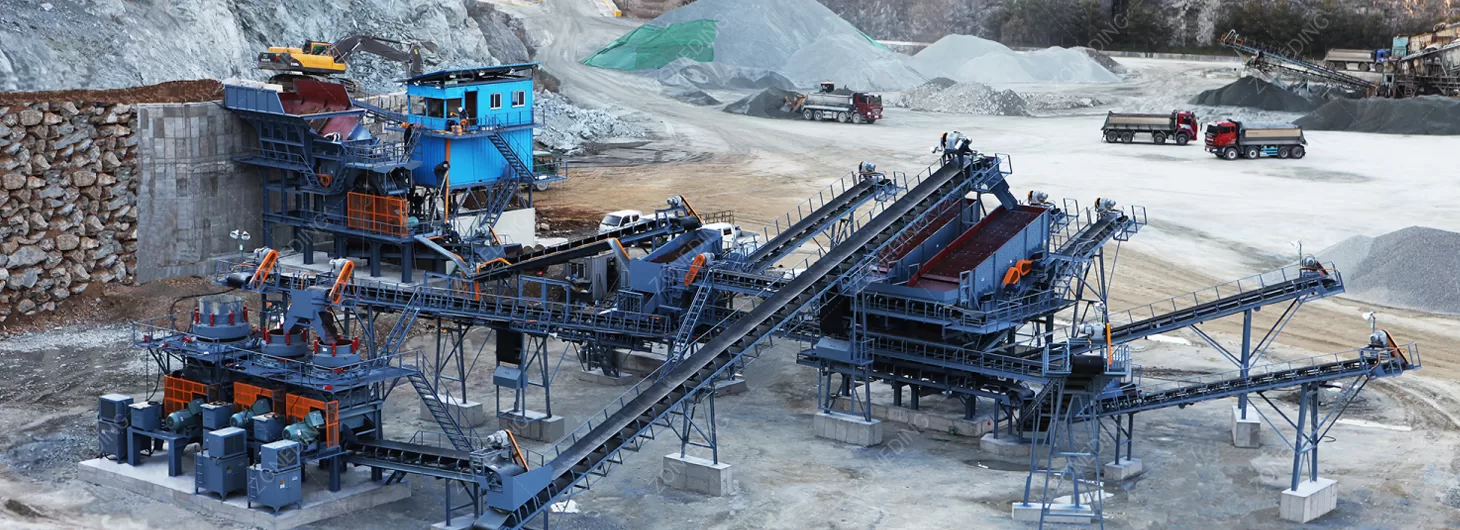
Anyone who understands the crushing industry probably knows that in addition to mobile crushing trucks, engineers usually analyze the customer’s needs and combine jaw crusher, cone crusher, impact crusher, feeding equipment and screening system to form a set of inconvenient “stationary” crushing plant. Here we see what is the difference between stationary and mobile crushing plant.
What Are The Differences Between Stationary And Mobile Crusher Plant
Mobile crusher plants are designed to be easily transported from one location to another, allowing them to be flexible and adaptable for various job sites. In contrast, stationary crusher plants are permanently installed at a specific location and cannot be moved.
Crusher mobile plant is typically quicker and easier to set up compared to stationary plant. It often comes with their own integrated transportation and assembly systems, whereas stationary plants require more time and effort for installation.
Mobile crusher plants offer greater operational flexibility since they can be easily moved and repositioned as needed. This allows for efficient use of equipment and resources, especially when dealing with multiple job sites or temporary projects. Stationary plants, on the other hand, are fixed in place and may have limitations in terms of adaptability to changing operational needs.
Stationary crusher plants generally have higher production capacities compared to mobile plants. This is because stationary plants can be optimized and customized for specific applications and large-scale operations, while mobile screening plant for sale prioritizes mobility and portability over maximum production capacity.
Stationary crusher plant requires a dedicated infrastructure, including foundations and supporting structures, which adds to the cost and complexity of installation. Mobile concrete crushing plant, on the other hand, has lower infrastructure requirements, often relying on existing roads or access points for operation.
It’s important to note that these differences may vary depending on specific models and configurations of crusher plants. The choice between stationary and mobile types depends on factors such as project duration, mobility needs, production requirements, and site conditions.
If you are interested in the stationary crushing plant, you can browse the following programs we have done for our customers.
150TPH Stationary Crusher Plant For Concrete Production
Configurations:
- Vibrating feeder
- Jaw crusher
- Impact Crusher
- Vibrating screen
Related Products
Tracked Cone Crusher
A Tracked Cone Crusher is a Cone Crusher – a compression-type crusher that breaks rock between a gyrating mantle and a stationary concave (bowl liner) – mounted on a tracked chassis with integrated power, feeding, and c...
Tracked Impact Crusher
A Tracked Impact Crusher is essentially an Impact Crusher (a machine that uses high-speed rotating blow bars to strike material, causing it to collide with impact plates and break) mounted on a tracked chassis, integrat...
Crawler jaw crusher
A crawler jaw crusher is a jaw crusher (a machine that uses two jaw plates to crush materials by squeezing) mounted on a self-propelled crawler chassis, integrated with feeding, conveying, and power systems. In mobile crushing op...
Mobile Cone Crusher
A mobile cone crusher is essentially a (device utilizing the principle of lamination crushing for medium-fine crushing) mounted on a mobile chassis (track or tire) and integrated with feeding, conveying, power, and other systems....
Mobile Impact Crusher
A mobile impact crusher uses a high-speed spinning rotor with "blow bars" (hammers) to strike feed material, breaking it along natural fissure lines. This differs significantly from mobile jaw crushers (compression between plates...
Tracked Mobile Screening Plant
A tracked mobile screening plant is a machine. It separates materials into different sizes. It has a screen box. It moves on tracks. It is built on a heavy frame. This frame lets it handle rough ground. It is easy ...
Mobile Crushing and Screening Plant
A Mobile Crushing and Screening Plant is a fully integrated system where crushing units (Stone Crusher), screening units (Vibrating Screen), feeders (Vibrating Feeder), and conveyors are all mounted on a single chassis or multipl...
Mobile Jaw Crusher
A mobile jaw crusher is essentially a (core equipment for primary material crushing) mounted on a movable chassis (track-mounted or wheeled), integrating auxiliary systems like feeding and conveying. Compared to stationary j...
loading...
已经是到最后一篇内容了!
What is a Mobile Crushing Station?
It integrates traditional stationary crushing equipment (like Jaw Crusher, Impact Crusher, Cone Crusher, screening machines, etc.) onto one or more movable chassis (wheeled or tracked). Its greatest advantage lies in the flexibility brought by "mobility," allowing it to be driven directly to the worksite, unlike stationary production lines that require foundations and lengthy installation/commissioning. This is revolutionary for projects with short cycles, dispersed sites, or those needing to follow the mining face.
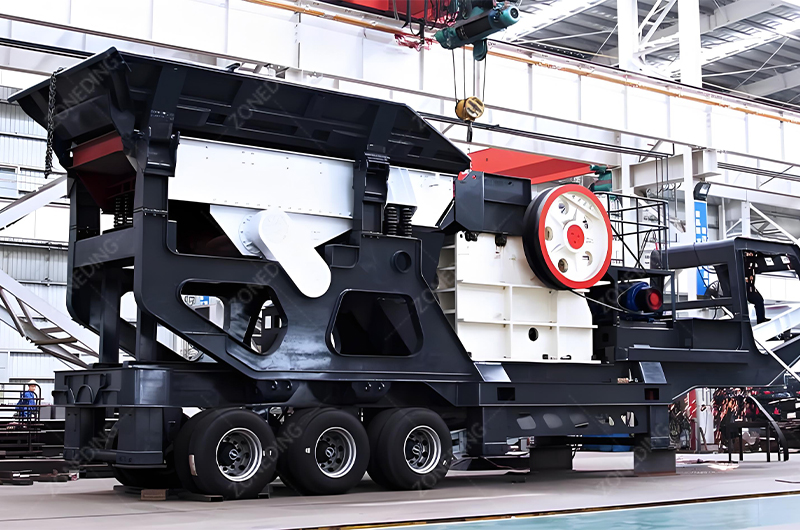
Table of Contents
- What Exactly is a Tracked Cone Crusher? Coarse or Fine Work in a Mobile Crushing Plant?
- Compared to Tracked Jaws or Impacts, What "Tough Stuff" Does a Tracked Cone Crusher Handle?
- What are the Real Benefits of "Tracked Mobility" for a Cone Crusher? Especially in Which Conditions?
- How Large a Rock Can a Tracked Cone Crusher "Eat"? How to Match Its Feed Opening to My Jaw Crusher's Output?
- How Fine Can It Crush Hard Rock? Product Shape? Can It Make Manufactured Sand?
- Extending Liner Life:
- Different Chamber Types (Coarse/Medium/Fine): Impact on Throughput & Liner Wear? How to Choose?
- Uneven Feed or Tramp Iron: Will the Cone Crusher "Strike" or Get Damaged? Protection Measures?
- Actual Hourly Throughput (Tons/Hour) of a Tracked Cone Crusher? What Factors Influence It?
- How to Perfectly Pair a Tracked Cone Crusher with a Mobile Screening Plant for Spec Product?
- Buying a Tracked Cone Crusher: Beyond Price, What Technical Parameters & Configurations are "King"?
- FAQ
How is a mobile crushing station better than a stationary crusher?
Besides flexible relocation and no need for foundations, mobile crushing stations also offer rapid commissioning, compact layout, integrated design, and strong adaptability.
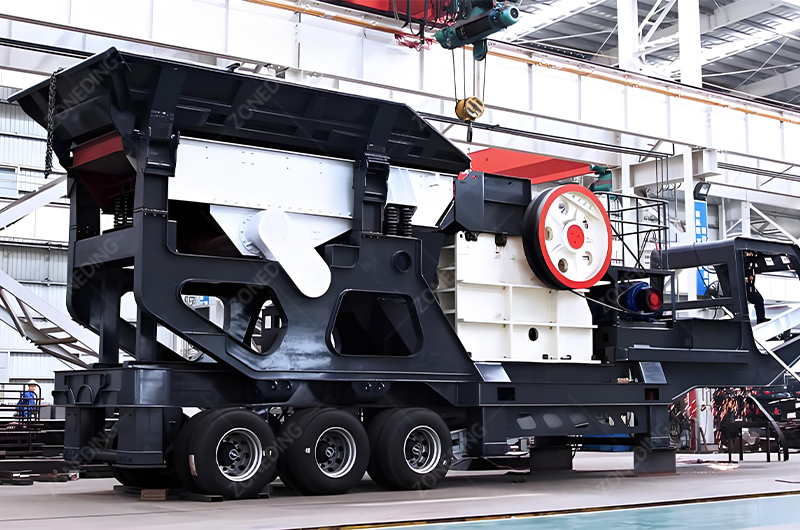
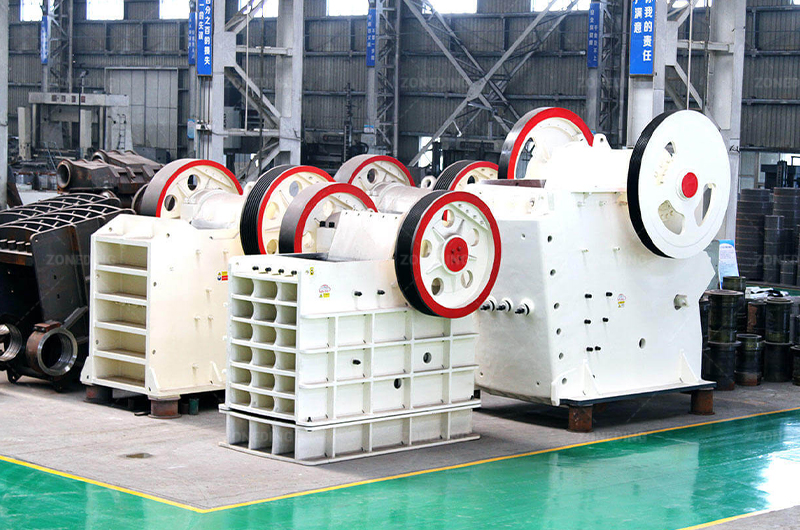
Practical Benefits of Mobile Crushing Stations:
- Saves Time Costs: Eliminates lengthy infrastructure and installation cycles, enabling rapid production and quick returns.
- Reduces Civil Investment: Saves significant civil engineering costs like foundations and plant buildings.
- Minimizes Material Re-handling: On-site processing reduces transport vehicles, fuel consumption, tire wear, and labor costs.
- Flexible Site Adaptation: Suitable deployment positions can be found whether on rugged mountains or confined construction sites.
- Environmental Benefits: Source processing reduces dust and noise pollution during material transport, making it easier to meet environmental regulations.
- Higher Equipment Resale Value: Compared to fixed equipment, mobile crushing stations, as independent units, are easier to trade second-hand and generally retain higher value.
Tracked vs. Wheeled Mobile Crushing Stations: Which "Legs" Suit You Better?
Choosing between tracked and wheeled mobile crushing stations mainly depends on your mobility needs and site conditions. Tracked units excel at short-distance movement and operation on rough, uneven terrain without extra traction; wheeled units are better suited for flat ground or situations requiring frequent medium-to-long distance road transport.
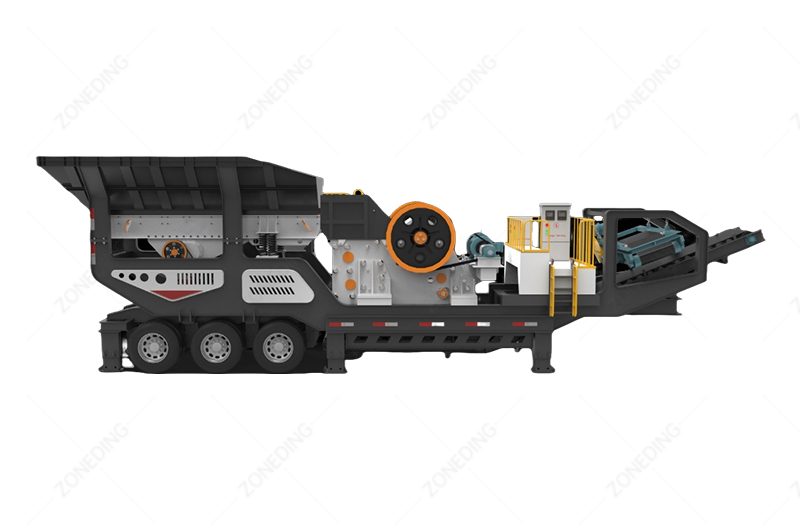
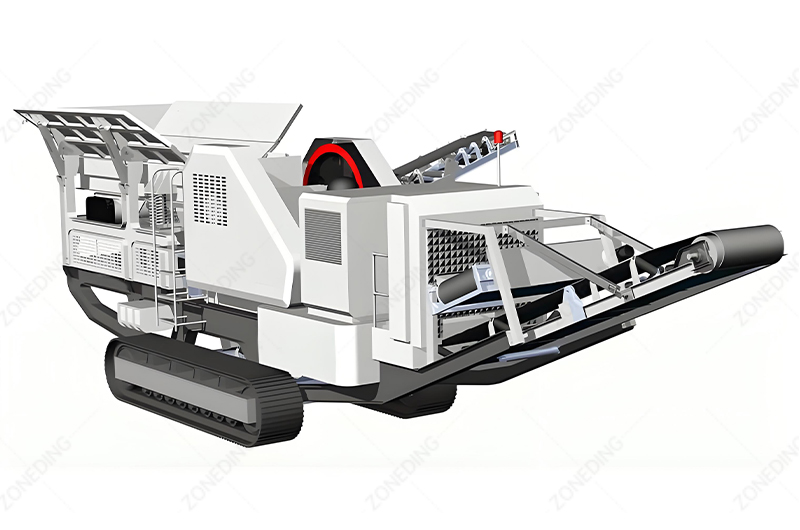
Think of a Tracked Mobile Crushing Station as a "tank." It can easily handle rugged mountain roads, muddy construction sites, and even climb certain slopes to operate, achieving true "crush-as-you-go." It moves using its own tracks, typically hydraulically driven and operable via wireless remote control, making it ideal for frequent short-distance repositioning within mines and quarries.
The wheeled type is like a "truck." It requires a tractor unit for movement but offers higher transport efficiency on paved roads and better compliance with road regulations, making it suitable for projects requiring frequent long-distance transfers between different sites, such as road construction or construction waste processing contractors. Its price is usually slightly lower than a tracked equivalent, but it requires relatively flat and firm operating ground, and needs support legs deployed for stability during operation.
Feature Comparison | Tracked Mobile Crushing Station | Wheeled Mobile Crushing Station | Practical Significance for You |
---|---|---|---|
Mobility | Excellent on-site mobility, adapts to rough terrain | Convenient road transport, suitable for long distances | Choose tracked for in-mine use, wheeled for inter-site moves |
Site Requirements | Lower requirements, can climb slopes | Needs relatively flat, firm ground | Tracked is more adaptable |
Relocation Method | Self-propelled tracks (short distance) | Requires tractor unit (long distance) | Tracked is convenient short-distance, wheeled efficient long-distance |
Deployment Time | Faster, remote control positioning | Faster, but needs tractor & leveling legs | Both faster than stationary, tracked more flexible for site micro-adjustments |
Initial Cost | Relatively higher | Relatively lower | Balance budget and primary application scenario |
Applicable Conditions | Large mines, quarries, harsh environments | C&D waste processing, road construction, site leveling | Tracked for heavy loads, slopes; Wheeled for multi-site, road network access |
Main Crusher Selection: Which Crusher "Heart" Suits Your Mobile Crushing Station?
The core of a mobile crushing station is the main crusher, commonly jaw, impact, or cone type. Which one to choose depends mainly on the material type and hardness you need to process, feed size, and requirements for the final product shape and gradation.
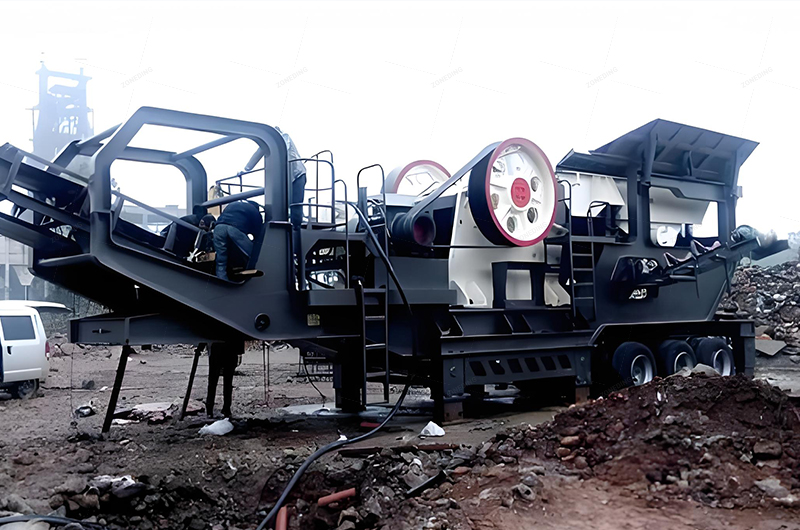
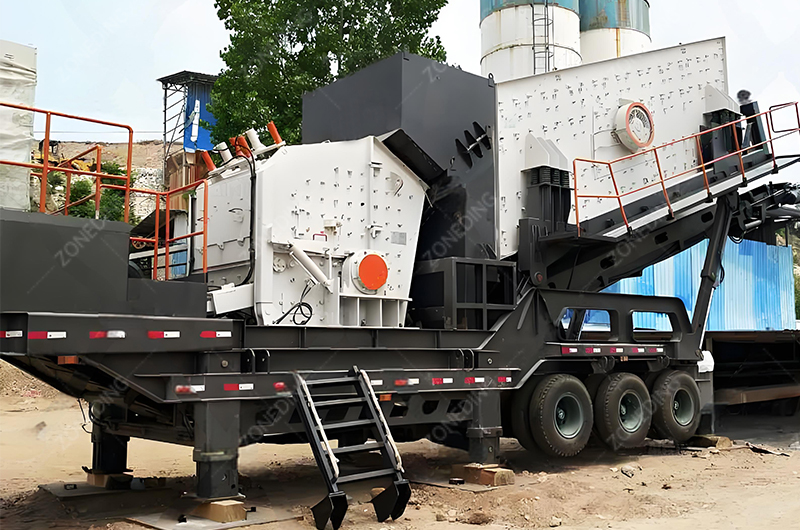
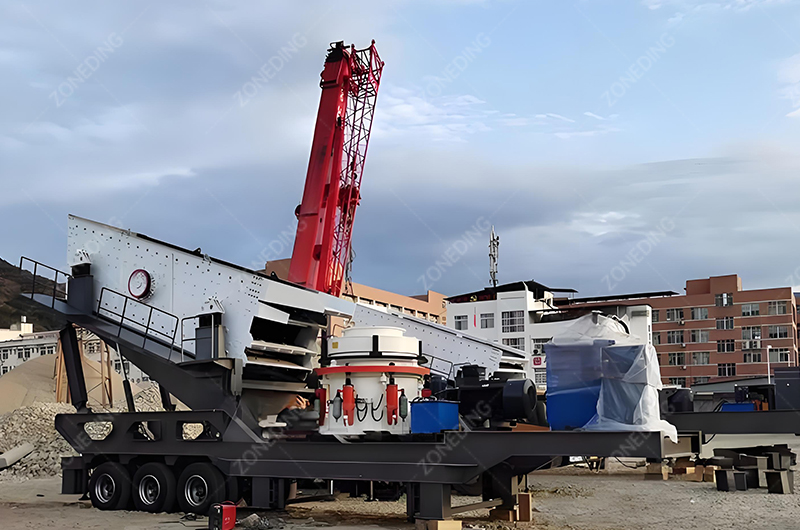
- Mobile Jaw Crusher: Like a strong "big eater," mainly used for primary crushing, handling large, hard materials (e.g., granite, river pebbles, iron ore). It features a large reduction ratio, simple and reliable structure, and relatively easy maintenance. If you need the first stage of crushing for large quarried rocks, a mobile jaw crusher is usually the first choice.
- Mobile Impact Crusher: Like a "shaping master," typically used for secondary or tertiary crushing, especially good at processing medium-hard or softer materials (e.g., limestone, concrete blocks, construction waste). Its advantage is excellent product shape (cubical), making it ideal for producing high-quality recycled aggregates or stone for road surfaces. However, its blow bars and impact plates are wear parts, wearing quickly with highly hard, abrasive materials (like river pebbles), leading to relatively higher operating costs. Pay special attention to rebar issues when processing construction waste (see Application Scenarios section).
- Mobile Cone Crusher: The "expert" for secondary and tertiary crushing of hard rock, suitable for crushing high-hardness, abrasive materials (e.g., granite, basalt, iron ore). It uses lamination crushing principles, produces good product shape, has high capacity, but is relatively complex in structure with higher purchase and maintenance costs. Often used after a jaw crusher for secondary or tertiary crushing.
How to Choose the Main Crusher Based on Needs?
- Processing Hard Rock (Granite, River Pebbles)?
- Primary Crushing: Mobile Jaw Crusher
- Secondary/Tertiary Crushing: Mobile Cone Crusher
- Processing Medium-Soft Rock (Limestone) or Construction Waste?
- Primary Crushing: Mobile Jaw Crusher
- Secondary/Tertiary Crushing (good shape required): Mobile Impact Crusher
- Secondary/Tertiary Crushing (high capacity required): Mobile Cone Crusher (also feasible, but higher cost)
- Extremely High Requirements for Final Aggregate Shape?
- Mobile Impact Crusher is the top choice (for low-to-medium hardness materials).
- For hard rock, a combination of Cone Crusher + Shaping Machine (VSI) can be used.
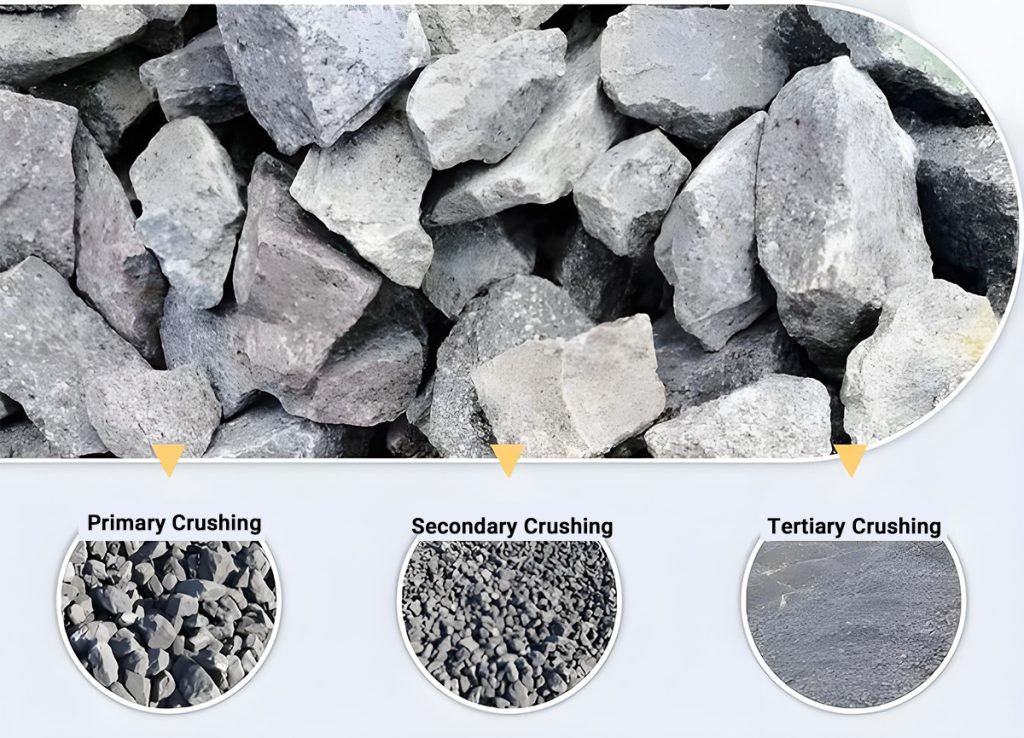
Application Scenarios for Mobile Crushing Stations: Can They Handle Everything from Ore to Construction Waste?
The application range of mobile crushing stations is very broad, covering almost all fields requiring material crushing. From hard rock mining and sand/aggregate production to urban construction waste crushing for recycling, earthwork projects, and road reconstruction, their presence is visible.
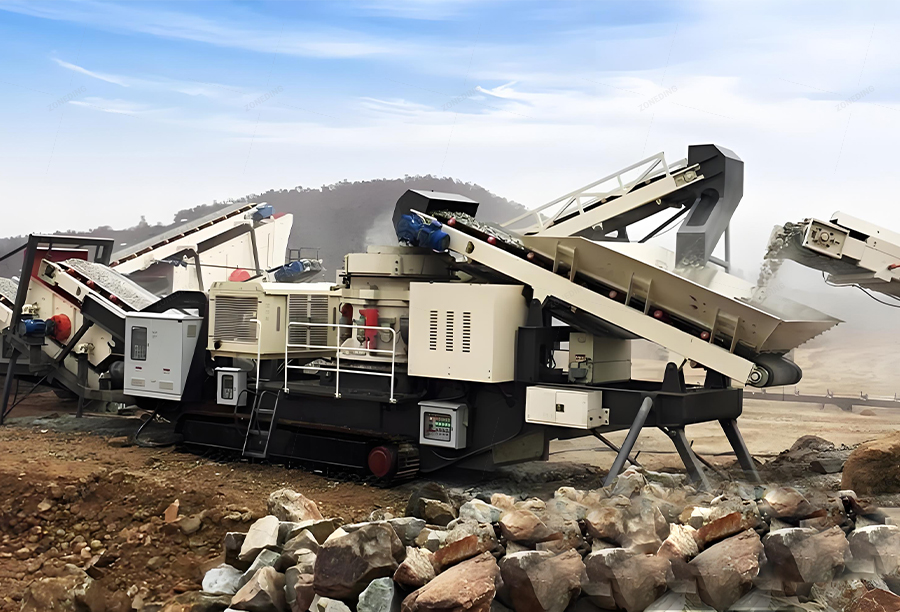
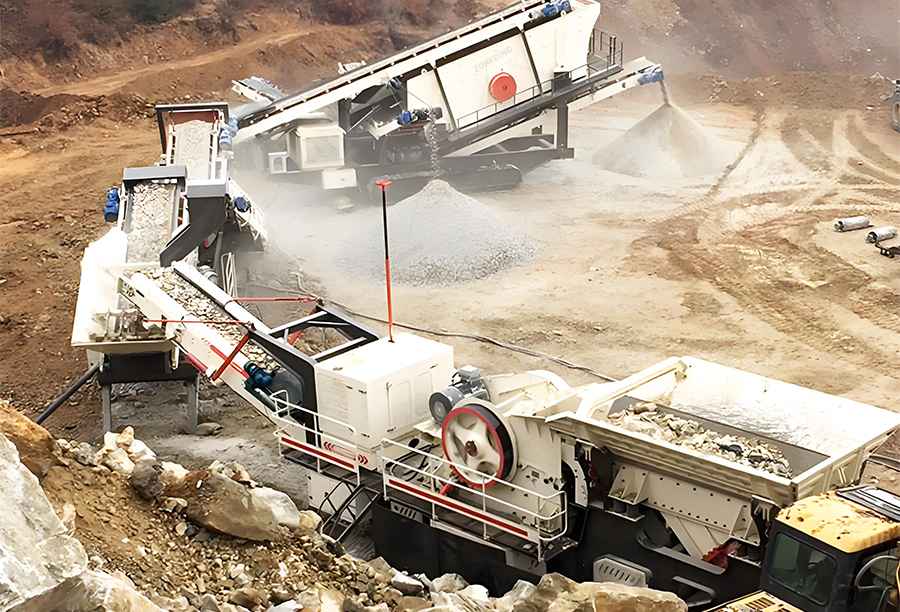
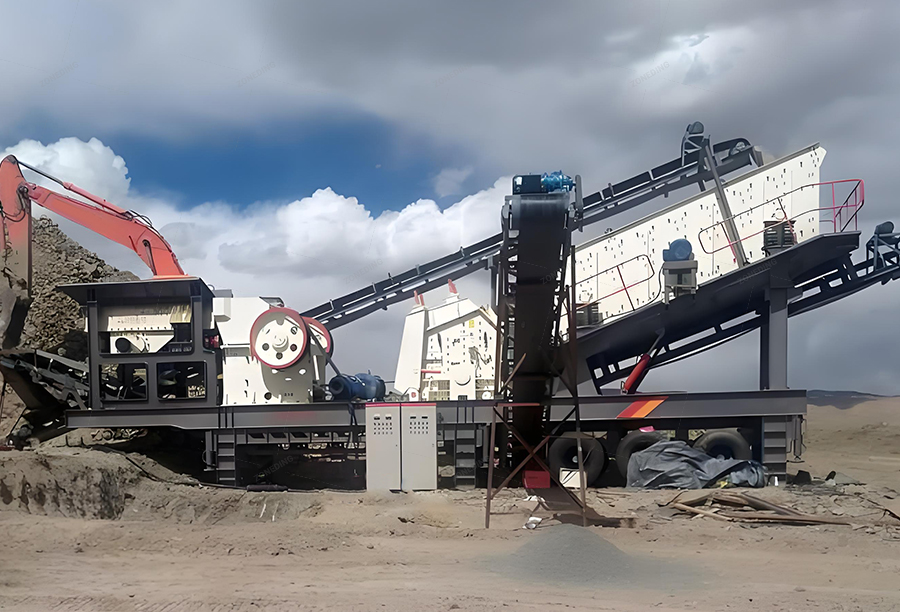
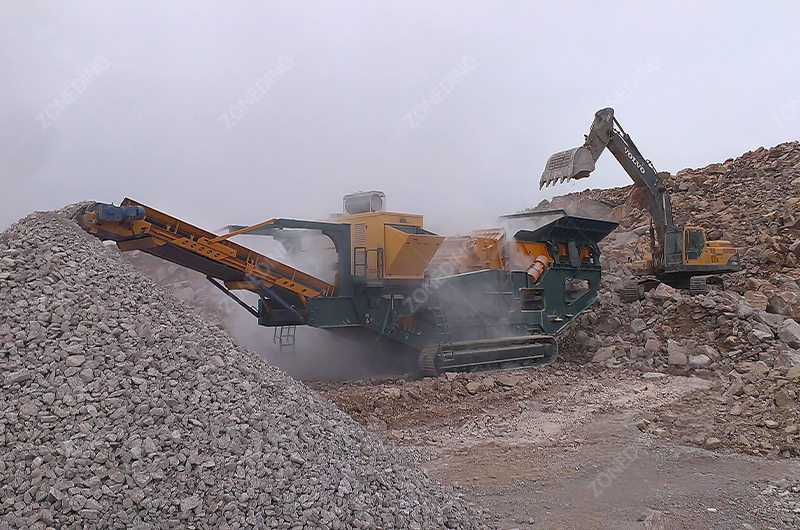
You can view the mobile crushing station as a versatile "material processing platform." Its core value lies in bringing the crushing process to the material's location, greatly expanding application boundaries:
- Mines and Quarries: Crushing ore directly near the working face, combined with conveyors, reduces internal transport costs (value of in-pit mobility).
- Sand and Aggregate Production: Flexible plant setup, quickly responding to market demand for manufactured sand and various aggregate specifications.
- Construction Waste Recycling: Fastest growing field. On-site processing of waste concrete, bricks, producing recycled aggregates.
- Earthworks and Road Construction: On-site processing of tunnel muck, old pavement materials, reducing external transport and enabling reuse in the project.
- Coal Mines: Crushing coal or gangue.
- Other Solid Waste Treatment: Such as industrial slag, tailings, etc.
How to Determine the Mobile Crushing Station Capacity You Need?
Determining the required capacity for a mobile crushing station involves considering your total project volume, planned duration, daily effective working hours, material characteristics (hardness, moisture, feed size, output requirements), and equipment combination efficiency. You cannot simply rely on the equipment's nominal maximum capacity.
Estimating capacity requires more than a guess; a simple calculation is needed:
Required Hourly Capacity (tons/hour) ≈ Total Project Volume (tons) / (Planned Duration Days × Daily Effective Working Hours × Efficiency Factor)
The "Efficiency Factor" here is key, typically ranging from 0.6 to 0.8, because the following factors affect actual output:
- Material Characteristics: Hardness, toughness, moisture content, and clay content all impact actual crushing efficiency.
- Feed and Output Requirements: Oversized feed or requirements for very fine output will reduce capacity.
- Pre-screening Efficiency : Poor pre-screening reduces the main crusher's efficiency.
- Equipment Matching and Operation : System bottlenecks, improper operation, and delayed maintenance significantly reduce capacity.
- Feed Continuity: Interruptions in material feeding directly impact output.
Building a Mobile Crushing Production Line: How to Efficiently Combine Multiple Units?
A single mobile crushing station often only completes a specific stage of crushing or screening. To form a complete production process (e.g., from large raw stone to multiple specifications of finished aggregate), multiple mobile units with different functions (like mobile jaw crusher + mobile cone crusher + mobile screening station) need to be combined and connected via conveyors, forming a Mobile Crushing and Screening Plant.
You can flexibly combine different mobile crushing units based on process requirements:
- Common Combo 1 (Processing Hard Rock):
Mobile Jaw Crusher
->Mobile Cone Crusher
->Mobile Screening Station
- Common Combo 2 (Processing Medium-Soft Rock/Construction Waste, Good Shape Required):
Mobile Jaw Crusher
->Mobile Impact Crusher
->Mobile Screening Station
- Common Combo 3 (Sand Making):
Mobile Jaw Crusher
->Mobile Cone Crusher
->Mobile Sand Making Machine
->Mobile Screening Station
Key to Efficient Combination ( System Engineering Perspective):
- Capacity Matching: Processing capacity (tons/hour) of each unit must be precisely matched to avoid bottlenecks. Downstream units usually have slightly higher capacity than upstream ones.
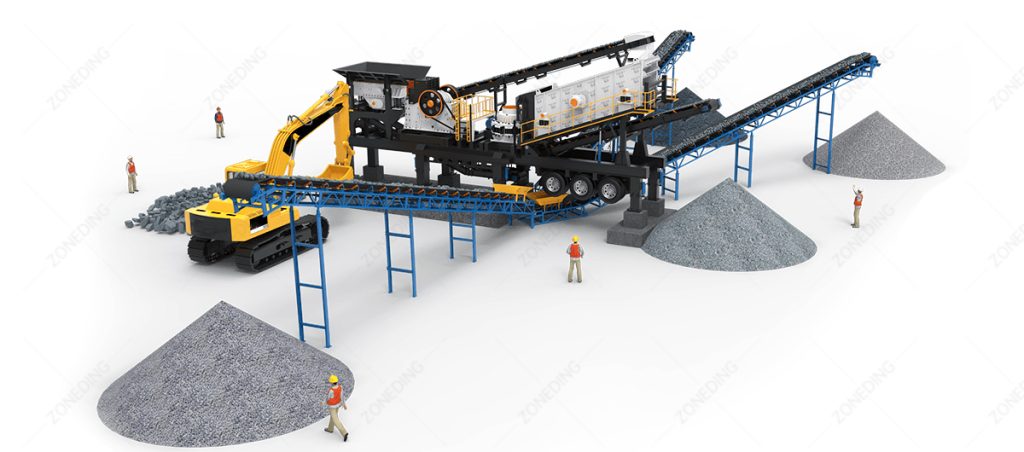
- Size Reduction Linkage: Optimal feed and discharge sizes between successive crushing stages must match.
- Smooth Material Flow: Conveyor belt design must be reasonable, preventing blockages and spillage.
- System Integration: All units (crushing, feeding, conveying, power, control) need to be considered as a whole; compatibility is crucial.
- Centralized Control: Modern production lines often feature integrated control systems for easy operation and monitoring.
- Site Layout: Plan placement and movement routes reasonably.
Key Factors When Buying a Mobile Crushing Station
When purchasing a mobile crushing station, price is important but should never be the sole consideration. Focus more on the equipment's reliability, performance stability, ease of maintenance, operating costs (fuel/power consumption, spare parts), manufacturer service, and suitability for your specific working conditions. A cheap but frequently failing, inefficient machine can ultimately cost far more than the initial investment.
Beyond the main crusher, capacity, and chassis type, the following points are "hardcore" indicators that must be thoroughly investigated during purchase, based on extensive practical experience:
- Main Crusher Performance & Durability: Crushing chamber design, wear part material life and replacement convenience, quality of key components (bearings, main shaft).
- Feeding & Pre-screening System : Capacity matching, smooth vibration, pre-screening effectiveness (is the grizzly bar design reasonable and adjustable?).
- Power System : Engine/motor brand reliability, fuel/power consumption level, availability of dual power options, emission standards.
- Hydraulic System: The "Nerve Center"! Focus on its response speed, precision (affects stable output and protection), contamination resistance, component brand quality, and integration with PLC intelligent control.
- Chassis & Structural Components : The "Unsung Hero"! Steel grade and thickness, weld quality, structural design (reinforcements, stress treatment) determine if the equipment can withstand long-term vibration and load in harsh conditions. Reliability of tracks/travel mechanism.
- Control System: Ease of operation, automation level (one-button start/stop, automatic overload adjustment), remote monitoring and diagnostic functions.
- Ease of Maintenance : Accessibility of maintenance points, space for replacing wear parts, skill requirements for maintenance personnel.
- Manufacturer Strength & Service: Brand reputation, successful cases, after-sales response speed, spare parts availability and price, training support.
Operating Costs & Maintenance of Mobile Crushing Stations
The main operating costs of mobile crushing stations include fuel/electricity bills, wear part replacement, routine maintenance, and labor. Fuel/power consumption depends on equipment power, load factor, and power system efficiency ; it cannot be generalized as high or low. Maintenance, compared to stationary plants, has higher requirements in some aspects (like hydraulic systems, compact spaces), but generally follows standard machinery maintenance principles.
Detailed Explanation:
- Fuel/Power Consumption:
- Diesel Drive: Fuel consumption is a major operating expense. High-efficiency, energy-saving engines and transmission methods (like diesel-electric drive) are preferable.
- Electric Drive (External/Generator/Dual Power): When feasible, significantly reduces energy consumption and maintenance costs, lowers emissions and noise. Preferred for long-term operations or environmentally sensitive areas.
- Actual Fuel/Power Consumption: Affected by load factor; optimizing production organization can lower average consumption.
- Maintenance:
- Routine & Periodic: Same as other construction machinery – check fluids, lubrication, fasteners, cleaning, filter changes, etc. Strictly follow the manual.
- Wear Parts: Jaw plates, blow bars, liners, screen meshes are major maintenance costs, requiring regular inspection and replacement.
- Challenges:
- Hydraulic System: High requirement for oil cleanliness, critical for maintenance.
- Maintenance Access: Compact design may make some areas hard to reach.
- Comprehensive Skills: Higher demands on operators' and maintenance personnel's electrical and hydraulic knowledge.
- Recommendation: Choose equipment with user-friendly maintenance design, value manufacturer training and technical support. Preventive maintenance is far better than breakdown repair.